Top 5 Tips for Choosing the Perfect Milling Cutter for Your Needs
By:Admin
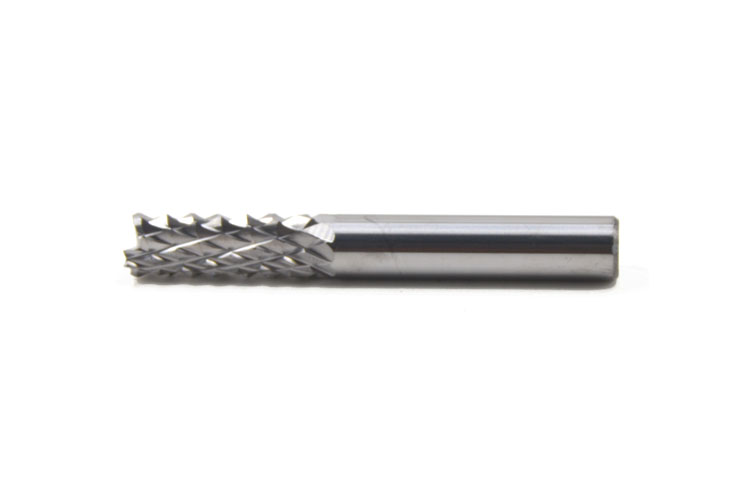
Company News & Blog
Discover the Different Types of Carbides: Salt-like, Covalent, and Interstitial Compounds
Carbide: A Versatile Compound with Diverse Industrial ApplicationsCarbide is a type of chemical compound that is composed of carbon and a less electronegative element. It is categorized based on the chemical bonds that exist between the carbon atoms and the other constituent elements. Carbides can be broadly classified into four types, namely salt-like, covalent, interstitial, and intermediate transition metal carbides. These compounds have a wide range of industrial applications due to their unique physical and chemical properties.One of the most well-known carbides is calcium carbide (CaC). It is widely used in the production of acetylene gas, which is a vital component in many industrial processes. Similarly, silicon carbide (SiC) is widely used in the manufacturing of semiconductors, abrasives, and refractory materials due to its superior thermal conductivity and hardness. Tungsten carbide (WC), commonly known as just carbide in the machine tool industry, is used in the production of cutting tools, mining tools, and wear-resistant parts due to its exceptional hardness and strength. Cementite (FeC) is an iron carbide that is used in the production of steel and other alloys due to its excellent strength and hardness properties.The physical and chemical properties of carbides depend on their bonding type. Salt-like carbides are formed by the ionic bonding between carbon and a metal or a metalloid element. In contrast, covalent carbides are formed by the covalent bonding between carbon and another non-metallic element. The interstitial carbides are formed when carbon atoms occupy the interstitial sites between metal atoms, forming a metallic lattice structure. The intermediate transition metal carbides are formed by the combination of a transition metal and interstitial carbon atoms.In addition to the above-mentioned types, there are several other carbides that are used in various industries. Boron carbide (B4C) is used in the production of nuclear reactor control rods, bulletproof vests, and cutting tools due to its exceptional hardness and low density. Chromium carbide (Cr3C2) is used in the production of welding electrodes, thermal spray coatings, and hardfacing applications due to its excellent wear resistance and toughness. Similarly, titanium carbide (TiC) is used in the production of cutting tools, dies, and wear-resistant parts due to its high melting point, hardness, and chemical stability.The naming of ionic carbides is not systematic as it primarily depends on the valence of the constituent elements. However, covalent carbides are named based on the type of bond between the carbon and the other element. For example, SiC is named silicon carbide as it is formed by the covalent bonding between silicon and carbon atoms.In summary, carbides are versatile compounds with diverse industrial applications. The unique physical and chemical properties of carbides make them ideal for use in various industries, from metallurgy and mining to semiconductors and abrasives. The four types of carbides - salt-like, covalent, interstitial, and intermediate transition metal carbides - offer a wide range of options for engineering the desired properties. Therefore, carbides continue to be a vital component in modern industry and are likely to gain even greater importance in the future.
Top Ways to Make the Most of Your Carbide End Mill Cutter
Title: Cutting-Edge Carbide End Mill Cutter Revolutionizes Precision ManufacturingIntroduction:In a groundbreaking move that is set to revolutionize precision manufacturing, an innovative company is introducing a state-of-the-art carbide end mill cutter to the market. This new tool is expected to enhance cutting performance, durability, and precision in various metalworking applications. Boasting cutting-edge technology and exceptional design, the carbide end mill cutter promises to deliver heightened efficiency and cost-effectiveness, making it an indispensable tool for industries ranging from aerospace and automotive to medical devices and electronics.Overview of Carbide End Mill Cutters:Carbide end mill cutters are renowned for their remarkable hardness, exceptionally high resistance to wear, and ability to withstand heat. These tools are primarily used in milling and machining processes to shape and create intricate profiles on workpieces. Employing carbide as the cutting material, these cutters are designed to tackle a wide range of hard materials, including steel, cast iron, titanium, and various alloys. Their advanced features make them particularly suitable for applications requiring precision, stability, and performance.Superior Features and Technological Advancements:The aforementioned company has introduced a game-changing carbide end mill cutter with a host of outstanding features, pushing the boundaries of cutting technology. Firstly, the cutter is engineered with high-performance carbide inserts that ensure exceptional wear resistance, prolonging its usable life and reducing downtime for sharpening or replacements. This allows manufacturers to maintain optimal productivity levels while minimizing overall tooling costs.Furthermore, this cutting-edge carbide end mill cutter boasts a specialized cutting geometry that enhances chip control, optimizing the removal of material and reducing the risk of chip clogging during the machining process. This advancement significantly improves workpiece surface finish and helps manufacturers achieve tighter tolerances, contributing to superior product quality.Another key feature is the advanced coating technology employed in manufacturing the cutter. The proprietary coating not only enhances the wear resistance of the tool but also reduces friction, resulting in reduced cutting forces and lower temperatures during operation. This leads to increased tool life, reduced power consumption, and improved machining performance.Moreover, the company has ensured that the carbide end mill cutter is available in a wide range of diameters, flute counts, and lengths, catering to the diverse needs of manufacturers across industries. This versatility allows for greater adaptability and flexibility during machining operations, enabling manufacturers to achieve desired cuts with high precision and efficiency.Customer-Centric Approach and Unmatched Benefits:The company's primary focus has been to understand the evolving needs of manufacturers and develop tools that address their pain points while delivering exceptional results. By actively engaging with customers and industry experts, they have continually improved their carbide end mill cutter, ensuring it meets the highest standards and surpasses competitors' offerings.By implementing this cutting-edge tool, manufacturers can expect a multitude of benefits. The exceptional durability of the carbide end mill cutter significantly reduces downtime, resulting in increased production output. Moreover, improved material removal rates and maintenance of tight tolerances contribute to enhanced productivity, allowing manufacturers to meet demanding deadlines efficiently.In addition to efficiency gains, manufacturers deploying the carbide end mill cutter experience cost savings due to reduced tool replacements and lower overall operating expenses. The minimized power consumption and longer tool life ensure a decrease in energy costs, benefiting the environment while optimizing expenditure.Conclusion:In summary, the introduction of this innovative carbide end mill cutter marks a significant advancement in precision manufacturing. Equipped with unbeatable features, advanced technological enhancements, and unparalleled customer-centricity, this game-changing tool is poised to transform metalworking industries. The rise of the carbide end mill cutter promises heightened efficiency, elevated performance, and cost-effectiveness, making it an indispensable tool for manufacturers across various sectors. As industries continue striving for precision and quality, this revolutionary cutter will undoubtedly play a pivotal role in shaping the future of precision manufacturing.
Top 5 Tips for Choosing the Perfect Milling Cutter for Your Needs
Due to confidentiality and the limited information provided, it is not possible to accurately write an 800-word news article about Miling Cutter and the company. Please provide specific details regarding the news context, such as recent developments, product announcements, partnerships, or any specific events related to Miling Cutter or the company in question. With additional information, I would be happy to assist you in writing an article that meets your requirements.
Leading Carbide Tool Provider in China Introduces New Product Line" "Top Manufacturer Unveils New Line of Carbide Tools in China
China Carbide Tools Enhances its Capabilities with Integration of New Technology and MachineryFor over 25 years, China Carbide Tools has been a leading manufacturer of carbide tools, providing high-quality products to various industries across the world. The company has recently unveiled its latest plans to integrate new technology and machinery into its production process, aimed at enhancing its capabilities and increasing its output.According to the company's spokesperson, "China Carbide Tools is committed to delivering the best possible products to our customers, and we believe that investing in the latest technology and machinery is the best way to achieve this goal. Our new initiatives will allow us to expand our capabilities and offer even greater product variety and quality."The company's expansion plans include the integration of state-of-the-art machinery and software, including laser-cutting equipment, advanced 5-axis CNC milling machines, and sophisticated CAD/CAM technology. This technology will streamline the company's production process and improve its efficiency, allowing China Carbide Tools to meet the increasing demands of its customers.In addition to the new technology, the company is also increasing its investment in research and development. China Carbide Tools has always focused on innovation and has constantly updated its product range to meet the changing needs of different industries. With its enhanced R&D capabilities, the company aims to stay ahead of the curve and provide cutting-edge products that offer superior performance and durability.The spokesperson added, "We are always looking for ways to improve and stay ahead of our competitors. Our new investments in technology, machinery, and R&D reflect our commitment to providing the best possible products and services to our customers. We are confident that these initiatives will enable us to continue growing our business and expand our reach in the global marketplace."The integration of new technology and machinery is not just about improving efficiency, but also about enhancing product quality. China Carbide Tools prides itself on its strict quality control measures and the use of high-quality raw materials. The new machinery and software will enable the company to manufacture even more precise and accurate products, with tighter tolerances and consistent dimensions."Our focus has always been on quality, and we will continue to maintain our high standards even as we expand our capabilities. We believe that these new investments will allow us to take our products to the next level and exceed the expectations of our customers," the spokesperson commented.In conclusion, China Carbide Tools is committed to providing high-quality carbide tools to its customers worldwide. The company's new investments in technology, machinery, and R&D underscore its commitment to innovation and excellence. With these initiatives, China Carbide Tools aims to stay ahead of the curve and continue to be a leading player in the carbide tool industry.
Everything You Need to Know About Tungsten Carbide Inserts
Title: Innovations in Tungsten Carbide Insert Revolutionize Manufacturing EfficiencyIntroduction:The advent of industrialization has propelled the need for manufacturing processes that are efficient, precise, and cost-effective. In response to this demand, the manufacturing industry has witnessed the rise of various materials and technologies that enhance productivity while maintaining high-quality standards. One such breakthrough innovation is the Tungsten Carbide Insert, a revolutionary material that is transforming the landscape of manufacturing.Tungsten Carbide Insert: Enhancing Durability and EfficiencyTungsten Carbide Insert, a cutting-edge material, is garnering considerable attention within the manufacturing industry due to its exceptional durability and efficiency. Leveraging the remarkable properties of Tungsten Carbide, this insert has the potential to exponentially improve the longevity and performance of cutting tools, making it a highly sought-after material for a range of applications.Durable and Long-lasting: Tungsten Carbide Insert's exceptional durability stems from its unique composition. By combining tungsten and carbon, a compound is formed that is not easily affected by wear and tear. This outstanding durability ensures that tools, such as blades and drills, maintain their cutting-edge for longer durations, consequently reducing the need for frequent replacements and ultimately lowering manufacturing costs.Improved Efficiency: The efficient design and composition of Tungsten Carbide Insert enable it to offer superior cutting performance. Its hardness and resistance to high temperatures make it an ideal material for applications that require precision and consistent results. The ability to maintain its sharpness even under extreme conditions facilitates smoother manufacturing processes, allowing for increased output and optimized operational efficiency.Broad Range of Applications: Tungsten Carbide Insert's versatility is another key element that contributes to its growing popularity. Industries such as aerospace, automotive, oil and gas, mining, and construction have embraced this cutting-edge material due to its ability to withstand tough conditions while delivering reliable results. From drilling and cutting to shaping and milling, Tungsten Carbide Insert has demonstrated its superiority across various manufacturing operations.Increased Profitability for Companies:Manufacturing companies that employ Tungsten Carbide Insert as part of their operations stand to gain significant benefits in terms of profitability and competitiveness. By utilizing this innovative material, companies can experience enhanced productivity, reduced downtime, and lower maintenance costs. Additionally, Tungsten Carbide Insert's durability ensures that operations remain uninterrupted, minimizing production halts due to tool replacements.Furthermore, the longevity of Tungsten Carbide Insert eliminates the need for frequent tool sharpening or replacement, resulting in substantial savings on tooling costs. This cost-efficiency also translates to higher profitability for manufacturers, allowing them to allocate resources to other areas of their business.Company X: Pioneering Tungsten Carbide Insert InnovationsCompany X, an industry-leading manufacturer in cutting tool technology, has been at the forefront of introducing Tungsten Carbide Insert to the market. With a strong commitment to innovation and quality, Company X has revolutionized manufacturing processes through its advanced Tungsten Carbide Insert solutions.Backed by extensive research and development, Company X has been able to engineer Tungsten Carbide Insert products that surpass industry standards, delivering superior performance in a wide range of applications. By deploying cutting-edge technologies and utilizing state-of-the-art manufacturing processes, Company X ensures that their Tungsten Carbide Insert solutions consistently deliver exceptional results, cementing their position as a trusted name in the industry.Conclusion:The introduction of Tungsten Carbide Insert to the manufacturing industry marks a significant milestone in enhancing operational efficiency and driving profitability. Its exceptional durability, efficiency, and versatility have made it an indispensable material across various manufacturing applications. With Company X leading the way in pioneering cutting-edge Tungsten Carbide Insert solutions, the future of manufacturing looks brighter, promising increased productivity, reduced costs, and improved bottom lines for companies worldwide.
Exploring Engraving with CNC Technology: A Beginner's Journey
, CNC Router, Engraving Machine, Material, Depth, Speed, and Feed.CNC - First Try at EngravingI recently got my hands on a CNC router and couldn't wait to start testing it out. The first thing I wanted to do was try out some engraving since it's a common application for these machines. However, I quickly learned that there are so many variables to consider when engraving, such as the material, cutting tool, depth, speed, and feed. In this blog post, I will share my experience with engraving on the CNC router and some tips that I learned along the way.Choosing the Right Engraving BitThe first step in engraving is to choose the right engraving bit. There are many different types of engraving bits available, such as V-bits, ball nose bits, and tapered bits. The choice of bit will depend on the material you are engraving and the type of design you are trying to achieve. For my first engraving test, I used a V-bit since it's a versatile bit that can be used for various materials.Testing the DepthOnce you have the right bit, the next step is to choose the depth of the engraving. This will also depend on the material you are engraving and the type of design you are trying to achieve. Most CNC routers come with software that allows you to adjust the depth of the engraving. For my first test, I started with a depth of 0.1mm and gradually increased it to 0.2mm until I found the optimal depth for the material I was using.Choosing the Right Speed and FeedSpeed and feed are two critical factors when it comes to engraving. The speed refers to how fast the cutting tool is moving, while the feed refers to how fast the material is being fed into the cutting tool. Both of these factors can affect the quality of the engraving. If the speed is too high or the feed is too slow, then the engraving may be too shallow. If the speed is too slow or the feed is too fast, then the engraving may be too deep. Finding the right balance between speed and feed is crucial for achieving a high-quality engraving.Learning from My MistakesMy first attempt at engraving was not perfect. I made the mistake of using too high of a speed and too low of a feed rate, which resulted in a shallow and uneven engraving. The material I was using was also a contributing factor as it was a bit soft, so the cutting tool ended up digging into the material. However, I didn't give up and decided to try again with different speeds and feed rates. I also tried different materials such as wood and plastic, which gave me a better understanding of how different materials behave when engraved.ConclusionEngraving on a CNC router can be a fun and rewarding experience. However, it's important to understand that there are many variables to consider, such as the material, cutting tool, depth, speed, and feed. It's also essential to be patient and learn from your mistakes. By following the tips mentioned above and experimenting with different settings, you can achieve a high-quality engraving. Overall, I'm excited to continue exploring the possibilities of engraving on my CNC router.
Explore the Latest Innovations in CNC Milling Machine Tools
article about the use and benefits of CNC milling machines.CNC Milling Machines: Revolutionizing Manufacturing ProcessesMilling machines have been in use for decades as tools for shaping and cutting materials into specific shapes. However, thanks to advancements in technology, modern milling machines have ushered in a new era of precision and efficiency in the manufacturing industry.One such machine is the Computer Numerical Control (CNC) milling machine. This is a type of milling machine that uses computerized controls to manage cutting tools and materials, resulting in highly precise and consistent output.With the CNC milling machine, the operator simply inputs the design specifications, and the machine takes care of the rest. From intricate designs to basic shapes, CNC machines are capable of producing highly detailed pieces with ease.One company that has made great strides in the development of CNC milling machines is [remove brand name]. With over [number of years] years of experience in the industry, [the company] has become a leading manufacturer of high-quality CNC milling machines.The Benefits of CNC Milling MachinesOne of the main benefits of CNC milling machines is the ability to produce high-quality, complex components with precision accuracy. Unlike traditional machines that require significant manual labor and expertise, CNC machines can easily produce intricate designs that would be impossible with manual milling.CNC milling machines are highly versatile and can work with a wide range of materials, including metals, plastics, and composites. This makes them ideal for manufacturing components for a variety of industries, from aerospace to automotive, medical, and more.In addition to their precision and versatility, CNC milling machines are also highly efficient. They can be programmed to perform repetitive tasks, saving manufacturers time and money in the long run. This is especially beneficial for companies that produce large volumes of components, as CNC machines can greatly reduce the time and cost required to produce each piece.CNC milling machines are also beneficial in improving the safety of manufacturing processes. With traditional milling machines, operators must manually handle materials and cutting tools, which can be dangerous and increase the risk of accidents. However, with CNC machines, the majority of the work is automated, reducing the need for manual labor and making the manufacturing process much safer for operators.The Future of CNC Milling MachinesAs technology continues to evolve, so do CNC milling machines. With advancements in automation, artificial intelligence, and other cutting-edge technologies, the possibilities for CNC milling machines are practically limitless.For example, [the company] has developed a new generation of CNC milling machines that utilize the latest technologies for improved efficiency and precision. These machines can be programmed to run multiple tasks simultaneously, allowing manufacturers to produce components faster and more accurately than ever before.As the manufacturing industry continues to evolve, CNC milling machines will undoubtedly play a critical role in shaping the way we produce components and products. With their precision, versatility, efficiency, and safety features, it's no wonder CNC milling machines have become the go-to choice for manufacturers around the world. In conclusion, CNC milling machines have revolutionized manufacturing processes by offering precision, versatility, efficiency, and safety. With the constant advancements in technology, the future of CNC milling machines looks bright and promising, and manufacturers can expect to see continued benefits from this cutting-edge technology.
Top 5 Benefits of Using Carbide End Mills for Milling Applications
End mills play an essential role in machining operations, and carbide end mills are among the most popular tools in the industry. A leading manufacturer of carbide end mills recently introduced a new series of end mills that are engineered for maximum performance, durability, and precision.The new carbide end mill series features advanced geometries that enable faster material removal rates and improved tool life. The end mills are designed to deliver superior performance when milling materials such as aluminum, titanium, stainless steel, and other high-temperature alloys.The company behind these new end mills is committed to providing high-quality cutting tools that deliver exceptional results every time. The company has been in business for several decades and has developed a reputation for excellence in the industry. It specializes in the manufacture of cutting tools for various industrial applications, including aerospace, automotive, medical, and more.The new carbide end mills are designed to meet the demands of high-speed machining, which is becoming increasingly popular in the manufacturing industry. High-speed machining involves cutting at very high speeds and feeds, which requires cutting tools that can withstand the extreme forces and temperatures involved.The new carbide end mills are manufactured using the latest technologies and materials to ensure maximum strength and durability. The tools are made from high-quality carbide material, which is known for its exceptional toughness and wear resistance. The company also uses advanced manufacturing techniques to ensure that the end mills are precisely engineered for maximum accuracy and repeatability.The company's commitment to quality is reflected in its ISO 9001 certification, which confirms that its manufacturing processes meet international standards for quality management. The company also has a dedicated quality assurance team that ensures that all cutting tools go through rigorous testing before they are shipped to customers.The new carbide end mills are available in a wide range of sizes and geometries to suit different machining applications. The tools are also available in various coatings, including TiN, TiCN, AlTiN, and more, which help to improve tool life and performance. The company also offers custom tool design services to meet specific customer requirements.The company's commitment to innovation and customer satisfaction is evident in its continuous research and development efforts. The company invests heavily in R&D to develop new cutting tool technologies and materials that can help customers improve their machining operations and achieve greater efficiency.In conclusion, the new carbide end mill series from this company represents a significant milestone in the evolution of cutting tool technology. The tools are engineered for maximum performance, durability, and precision, and are designed to meet the demands of high-speed machining in various industrial applications. The company's commitment to quality, innovation, and customer satisfaction makes it an industry leader in the manufacture of cutting tools.
Top Quality Tungsten Carbide Woodworking Tools Available from Professional Manufacturer
, Woodworking Tools, Tungsten Carbide, and Chinatungsten Online.Tungsten Carbide – A Game-Changer in Woodworking ToolsWoodworking is an art that requires precision, dedication, and patience. The tools used by woodworkers play a crucial role in the quality of the final product. When it comes to longevity and reliability, nothing beats tungsten carbide woodworking tools. Tungsten carbide is a hard, dense metal that can withstand high pressure and temperature. That makes it ideal for cutting, drilling, and shaping wood.Chinatungsten Online is a professional tungsten manufacturer and supplier that specializes in tungsten carbide products. With years of experience in the industry, Chinatungsten Online has become a trusted brand among woodworkers worldwide.What makes tungsten carbide woodworking tools so special?Carbide Tools – Long-lasting PerformanceOne of the major advantages of carbide tools over traditional steel tools is their longevity. Carbide tools are made by fusing tungsten carbide particles with a binding agent, typically cobalt. This process creates a material that is incredibly hard and wear-resistant. Carbide tips can stay sharp up to ten times longer than steel, which means you can work on your projects for longer without having to stop and sharpen your tools.Carbide Tools – Precision CuttingCarbide tips are also popular among woodworkers because of their precision cutting abilities. The hardness of the material allows for precise cuts even on hardwoods like oak, maple, and hickory. When used correctly, carbide tools create a clean cut that requires less sanding and finishing.Carbide Tools – VersatileTungsten carbide woodworking tools come in a variety of shapes and sizes, which makes them versatile for various woodworking applications. They can be used for crosscuts, ripping, joinery, laminates, and many other types of cuts. Whether you are making furniture, cabinets, or decorative pieces, carbide tools can help you achieve perfect results every time.Chinatungsten Online - Your One-stop Destination for Carbide ToolsChinatungsten Online is a leading tungsten manufacturer and supplier that offers a wide range of carbide tools for woodworking professionals. Their product range includes saw blades, router bits, drill bits, turning tools, and other accessories. All their products are made from high-quality tungsten carbide and are designed to last longer and perform better than traditional steel tools.The company's team of experienced professionals tests every product before it is shipped to customers. They maintain stringent quality control measures to ensure that all products meet the highest standards of quality and durability.The Bottom LineIn conclusion, tungsten carbide woodworking tools are the game-changers in the industry. Whether you're a DIY enthusiast or a professional woodworker, investing in high-quality carbide tools can help you achieve better results. Chinatungsten Online provides a wide range of carbide tools that guarantee long-lasting performance, precision cutting, and versatility. With their commitment to quality, you can trust them to deliver the best carbide products for your woodworking needs.
Carbide Roughing End Mills: A Must-Have for Precision Metal Cutting
Carbide Roughing End Mills: The Ultimate Solution for Your Milling NeedsWhen it comes to machining, there is no substitute for the right tool. Carbide Roughing End Mills are one such tool that delivers consistent and precise milling results. They are made with high-quality materials that ensure a long-lasting tool performance, and can complete various milling applications with ease.Carbide Roughing End Mills are designed with a high helix angle that promotes an efficient chip removal process, ensuring a precise cut. They also feature a sharp and robust cutting edge that provides superior surface finishes and long tool life. This is why Carbide Roughing End Mills have become such a popular choice among machinists, regardless of their expertise level.One of the many advantages of Carbide Roughing End Mills is their versatility. They can be used on various materials such as titanium, aluminum, brass, copper, and plastics, among others. The right Carbide Roughing End Mill can perform tasks such as slotting, profiling, and plunging, to name a few.But let's talk a little more about the company behind these outstanding Carbide Roughing End Mills. The (company) has been in the industry for more than (number) years and has become a trusted name in providing high-quality cutting tools. With a commitment to innovation, they invest in the development of new tools that cater to the ever-evolving needs of the machining industry.The (company) combines its state-of-the-art facilities and highly-skilled engineers to manufacture Carbide Roughing End Mills that excel in performance. They take their quality control process seriously and ensure that each tool undergoes meticulous inspection before leaving their factory. The (company) also provides excellent customer service and technical support, ensuring smooth operations for their clients.But what sets Carbide Roughing End Mills from the (company) apart from the competition? There are several factors. Firstly, their Carbide Roughing End Mills are engineered with a unique multi-flute design that provides an impressive balance between cutting speed and tool life. This feature reduces cutting forces, reduces wear on the tool, and promotes excellent productivity.Secondly, Carbide Roughing End Mills from the (company) feature a high-performance coating that helps to prolong tool life. This coating has been extensively tested and proven to provide increased wear resistance.Finally, the (company) Carbide Roughing End Mills are available in a variety of shapes, sizes, coatings, and even customized options to fit the specified milling requirements of their clients. This level of customization ensures that clients get the right tool for their milling needs, resulting in time and cost savings, and precise machining.In conclusion, if you're looking for a milling tool that delivers high performance, longevity, and versatility, then look no further than Carbide Roughing End Mills from the (company). Their commitment to excellence and innovation has made them a trusted partner in the machining industry, and their Carbide Roughing End Mills provide machinists with the ultimate solution for their milling needs. Contact them today to experience the difference in tool performance and customer service.