High-performance Milling Cutters with Micro Carbide Material
By:Admin
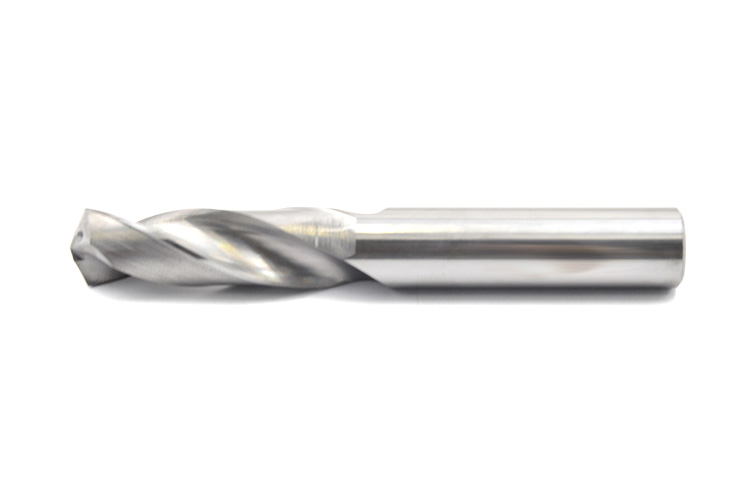
Introduction:
In the ever-evolving world of precision machining, advancements in cutting technology play a crucial role in enhancing performance and increasing efficiency. One such groundbreaking innovation is the Micro Carbide Milling Cutter, developed by a leading industry player.
Paragraph 1:
The anonymous cutting tools manufacturer has recently unveiled their latest creation, the Micro Carbide Milling Cutter. This state-of-the-art tool is poised to revolutionize the precision machining industry, enabling manufacturers to achieve unprecedented levels of precision, accuracy, and efficiency in their machining processes.
Paragraph 2:
The Micro Carbide Milling Cutter boasts exceptional strength and durability due to its unique composition of ultra-hard micro carbide material. This revolutionary material ensures that the cutter maintains its sharpness and cutting performance even under the most demanding conditions. Designed to be versatile, it is suitable for a wide range of materials including steel, aluminum, titanium, and various alloys.
Paragraph 3:
Moreover, the advanced manufacturing techniques employed in the production of the Micro Carbide Milling Cutter ensure consistently high-quality tools with exceptional dimensional accuracy, surface finish, and overall tool life. This reliability enables manufacturers to optimize their production processes, reduce downtime, and ultimately maximize profitability.
Paragraph 4:
The Micro Carbide Milling Cutter is engineered with special geometries and cutting-edge coatings that facilitate swift chip evacuation and efficient material removal. These features allow for high-speed machining while maintaining superior surface finishes, decreasing cycle times, and lowering overall manufacturing costs. The cutter's precision alignment ensures accurate and repeatable results, making it an invaluable tool for intricate machining tasks.
Paragraph 5:
The anonymous cutting-tool manufacturer realizes the importance of customization in meeting diverse customer requirements. Therefore, they offer a wide range of sizes, configurations, and cutting-edge variants for the Micro Carbide Milling Cutter. This ensures that manufacturers can select the ideal tool for their specific application, further enhancing productivity and maximizing performance.
Paragraph 6:
In addition to its remarkable performance and reliability, the Micro Carbide Milling Cutter is designed to prioritize operator safety. The manufacturer has incorporated advanced safety features, including noise reduction, vibration dampening, and enhanced coolant flow, thereby creating a safer working environment for machinists.
Paragraph 7:
The launch of the Micro Carbide Milling Cutter marks a significant milestone in the precision machining industry, establishing a new benchmark for performance, precision, and productivity. It is anticipated to garner widespread adoption in a myriad of manufacturing sectors ranging from automotive and aerospace to medical device fabrication and beyond.
Conclusion:
The introduction of the Micro Carbide Milling Cutter offers a glimpse into the future of precision machining, where cutting-edge technology and advanced materials converge to redefine industry standards. With its exceptional strength, durability, and performance, this innovative tool promises to revolutionize machining processes worldwide, enabling manufacturers to achieve unparalleled levels of precision and efficiency.
Company News & Blog
What is a Rotary Tool-Steel Cutter Used in Milling Machines?
Metal Milling Cutter: An OverviewEvery manufacturing process involves various cutting tools and machines. Among the most commonly used tools in the industry is the milling cutter. A milling cutter is a cutting tool used in a milling machine that is designed to shape, cut, and dress metal surfaces. In this blog, we'll cover the basics of milling cutters, their types, and applications.What is a Milling Cutter?A milling cutter is a rotating cutting tool that is mounted on a milling machine spindle. It is designed to remove material from a workpiece by advancing or rotating the cutter into the workpiece. The material removal process is achieved through the cutting edges on the milling cutter. These edges can be a combination of lips, flutes, teeth, or other features.Milling cutters come in various shapes and sizes and are made of different materials, including high-speed steel, cobalt, carbide, and diamond-coated. These cutters are selected based on the type of material to be machined and the desired surface finish.Types of Milling CuttersThere are many different types of milling cutters available in the industry. Here are some of the most popular ones:1. End MillEnd mills are among the most commonly used milling cutters. They are designed for cutting slots, profiling, and contouring. End mills come in a variety of shapes and sizes, such as square, ballnose, and corner radius.2. Face MillFace mills are designed to machine flat surfaces, and they have a large surface area compared to other milling cutters. The cutting edges are located on the face of the mill, and they produce a flat finish.3. Ball Nose CutterBall nose cutters are designed for producing rounded contours in a workpiece. They have a hemispherical shape with two cutting edges.4. T-slot CutterT-slot cutters are used for milling slots with a T-shaped profile. They have a straight shank with a T-shaped cutting edge.Applications of Milling CuttersMilling cutters are used in various applications, including:1. Machining complex shapesMilling cutters are often used to machine complex shapes that would be difficult or impossible to achieve with other cutting tools.2. High-precision machiningMilling cutters are capable of producing high-precision finishes on workpieces. They can be used to achieve tight tolerances on machined surfaces.3. Mass productionMilling cutters can be used in mass production processes to machine large quantities of parts. They are efficient and produce consistent results.ConclusionMilling cutters are essential cutting tools in the manufacturing process. They are designed to shape, cut, and dress metal surfaces with precision and efficiency. There are various types of milling cutters, including end mills, face mills, ball nose cutters, and T-slot cutters, each with unique features and applications. Selecting the right milling cutter for the job is crucial to achieve the desired surface finish and efficiency in the machining process.
Effective Cutting Tools for CNC Machines: A Comprehensive Guide
CNC Machine Cutting Tools Redefines Precision Engineering in the Manufacturing IndustryAs one of the core components in modern-day advanced manufacturing, cutting tools play a crucial role in producing high-quality precision components and parts. Talking of cutting tools, several leading companies have become the go-to provider, with one such company being a global leader in the design, manufacturing, and supply of CNC machine cutting tools.In its quest to redefine precision engineering in the manufacturing industry, the company has made significant strides in the development of cutting-edge CNC machine cutting tools. The tools are designed to deliver precision and accuracy while ensuring cost-effectiveness, making them an ideal choice for manufacturers looking to increase productivity and efficiency.The CNC Machine Cutting Tools are manufactured under stringent quality control measures, with every tool undergoing rigorous testing to ensure optimal performance. Moreover, the tools are designed to cater to different machining operations, such as turning, milling, drilling, and grinding. This capability makes the cutting tools versatile and adaptable, ensuring that manufacturers can handle a variety of CNC machining tasks with ease.Apart from quality and versatility, the CNC machine cutting tools are also designed to be user-friendly. The company has done an excellent job of keeping up with technological advancements, incorporating features that enhance ease of use, such as automation, digitalization, and connectivity.One such tool that has caught the attention of many manufacturers is the company's latest CNC machine cutting tool. The tool is designed to machine ports and ribs in engine blocks, providing precision and accuracy beyond what traditional cutting tools can achieve. The tool's unique design and cutting geometry make it effective in roughing the ports and ribs at higher speeds, reducing machining time and increasing efficiency.Additionally, the tool's advanced coating technology enhances its wear resistance properties, reducing the need for frequent tool replacement. The coating also improves the tool's chip evacuation properties, ensuring that manufacturers can maintain high machining speeds without clogging issues.Another notable feature of the CNC machine cutting tools is the the company's commitment to sustainability. Over the years, the company has developed sustainable machining solutions that reduce waste, energy consumption and enhance efficiency, all geared towards improving the planet's well-being.For instance, the cutting tools are designed to reduce the amount of coolant used during machining, eliminating the need for chemical disposal. Additionally, the tools' advanced cutting capabilities and high machining speeds reduce machining time, ensuring that manufacturers can complete their projects fast without wasting unnecessary materials.In conclusion, CNC machine cutting tools have become an integral part of modern-day advanced manufacturing. As the demand for high-quality precision parts continues to increase, companies that provide innovative and efficient cutting tools such as the global leader in the design, manufacturing and supply of CNC machine cutting tools will continue to thrive. With a notable commitment to quality, versatility, and sustainability, the company is well poised to deliver precision engineering solutions that redefine the manufacturing industry.
If you're new to the world of machining, purchasing end mills for the first time may be an overwhelming experience. With so many different options available, it can be difficult to know where to start or how to choose the right end mill for the job. In this blog post, we will cover what you need to know before you buy end mills for sale.End mills are rotary cutting tools that are used to remove material from a workpiece. They come in a variety of shapes and sizes, each designed to perform a specific function. The most common materials used to make end mills include high-speed steel (HSS), carbide, and cobalt.Before you begin your search for end mills for sale, there are a few key considerations you should keep in mind. These include:1. Material Type: The material you will be cutting will determine the type of end mill you need. For instance, working with stainless steel will require a different type of end mill than working with aluminum. Make sure you select an end mill that is designed specifically for the material you will be cutting.2. Coating: Many end mills come with a coating on the flute that can help extend the life of the tool. Coatings can include titanium nitride (TiN), titanium carbonitride (TiCN), and aluminum chromium nitride (AlCrN) among others. Choosing the right coating for your application will depend on the material you are machining and the type of cut you need to make.3. Flute Type: The number and type of flutes on an end mill will determine the speed and finish of the cut. A single flute end mill will remove material quickly, but may leave a rough finish. A four flute end mill will remove material more slowly, but will produce a smoother finish. The type of flute you need will depend on the job you are performing.4. Shank Size: The shank size of your end mill will determine if it is compatible with your milling machine. Make sure you are aware of the shank size you need before you make your purchase.5. Brand Reputation: Finally, make sure you are purchasing from a reputable brand. Look for reviews of the brand and specific end mill you are considering to ensure they are dependable and of high quality.When it comes to end mills for sale, there are many different options available. By keeping these key considerations in mind, you can choose the right end mill for your job with confidence. Whether you are a seasoned machinist or a beginner, selecting the right end mill will help you achieve the results you are looking for.
Rewritten SEO title: Essential Router Accessories - Ball Nose End Mills for Precision Cutting
End mills play an important part in the world of machining and the development of industrial applications. Ball nose end mills, in particular, are a vital tool used in industries like aerospace, automotive, and mechanical engineering. Made from high-speed steel or carbide, these essential cutters enable precise and efficient machining for optimal performance.Ball nose end mills are named so because of their distinct round-ended flutes and cutting edges, creating a “ball-nose” appearance. These tools are designed to create contoured surfaces and complex shapes with high accuracy, thanks to their unique cutting geometry. The flute design of a ball nose end mill helps to reduce the cutting force and friction during machining, enabling smoother and more efficient cutting.The Benefits of Using Ball Nose End Mills1. Precise Machining: Ball nose end mills are designed to create high precision milling surfaces. Their unique geometry helps to achieve a smoother surface finish, especially on complex and intricate shapes.2. Versatile: Ball nose end mills can be used for a wide range of applications, including contouring, slotting, and profiling.3. More Efficient: These end mills can remove material more efficiently by minimizing the amount of cutting force required during machining, resulting in higher speeds and feeds. More material can be removed in less time without compromising accuracy.4. Durable: Ball nose end mills are typically made from carbide or high-speed steel, making them highly resistant to wear and tear. This construction allows for extended tool life, reducing the cost and number of required tool replacements.Router Parts And Accessories for Ball Nose End MillsTo achieve optimal performance and longevity, it’s essential to pair your ball nose end mills with the right router parts and accessories. Here are some of the top accessories for ball nose end mills:1. End Mill Holders: These holders securely grip the end mill shank and help to reduce vibration and tool runout. This, in turn, produces better surface finishes and improves overall accuracy.2. CNC Tooling Systems: These systems include end mill holders, collets, and chucks, and are designed to fit a wide range of CNC machines. They provide a rigid and secure hold, maximizing the accuracy and precision of your machining.3. Carbide End Mill Sets: Carbide end mill sets are ideal for those who perform a variety of milling tasks. They offer versatility to the user, making it easier to switch between materials and applications.4. Coolant Delivery Systems: Keeping the cutting edges of your ball nose end mill cool is essential to extend its life and optimize performance. Coolant delivery systems help to flush away chips and debris, maintain consistent cutter temperatures, and improve surface finishes.Final ThoughtsIn the world of machining, choosing the right cutting tool can make all the difference in the quality, accuracy, and efficiency of your work. Ball nose end mills are an essential tool for creating precise and complex shapes while maintaining high accuracy. With proper care and maintenance, these end mills can provide long-lasting and efficient machining solutions. Don’t forget to use the right router parts and accessories to maximize your milling performance.
Top-Quality Two-Flute Upcut CNC Bits for Excellent Routing Results
Two Flute Upcut CNC Router Bits: The Perfect Solution for Smooth and Accurate RoutingThe world of CNC routing is an exciting one, with computer-controlled machines helping businesses and individuals create intricate designs with the utmost precision. However, to achieve the desired results, one crucial component that requires close attention is the router bit. Your choice of router bit can make or break the quality of your finished product. This is where two flute upcut CNC router bits come into play.What Are Two Flute Upcut CNC Router Bits?Two flute upcut CNC router bits are a specific type of cutting tool designed for use in CNC machines. They feature two spiral upcut flutes, which means that as the bit rotates, it pulls chips up and away from the workpiece. The upcut design helps to maintain a smooth and clean edge on the material, reducing fraying and leaving a polished finish.Benefits of Two Flute Upcut CNC Router BitsThere are several benefits to using two flute upcut CNC router bits, some of which include:1. Clean and Smooth FinishUpcut bits tend to offer a cleaner cut than their downcut counterparts. The upcut design pulls chips up and out of the way, reducing the chance of chip buildup. This results in less fraying, a smoother finish, and less clean-up work required after routing.2. Reduced Heat BuildupAnother advantage of two flute upcut CNC router bits is that they have an optimized geometry that helps reduce the amount of heat generated during cutting. This is important as excessive heat can lead to premature wear and tear on the bit, as well as cause cracking and warping of the material being routed.3. VersatilityTwo flute upcut CNC router bits are suitable for most routing applications, meaning that they can be used on a wide range of materials. These include wood, plastic, and some soft metals.Things to Consider When Choosing Two Flute Upcut CNC Router BitsWhen it comes to selecting the right two flute upcut CNC router bit for your project, there are several factors to keep in mind. These include:1. Bit SizeThe size of the bit you choose will depend on the scale of your project and the material you're using. Smaller bits are suitable for intricate work with fine details, while larger bits are ideal for roughing out and removing larger amounts of material quickly.2. Bit MaterialThe material your bit is made from will impact its durability and cutting performance. Common materials used to make router bits include carbide, high-speed steel (HSS), and cobalt.3. Flute LengthThe flute length of the bit refers to the length of the cutting portion. Longer flute lengths are better for deeper cuts, while shorter flute lengths work well for shallower cuts.Tips for Using Two Flute Upcut CNC Router BitsHere are some tips to help you get the most out of your two flute upcut CNC router bit:1. Choose the Right Speed and Feed RateThe speed and feed rate at which you run your CNC machine can have a significant impact on the performance of your bit. Be sure to follow the manufacturer's recommended speed and feed rate for your specific bit.2. Keep Your Bit SharpDull bits can cause excessive heat buildup and lead to a rough finish. Be sure to sharpen your bit regularly to maintain optimal performance.3. Clean Your Bit After UseAfter routing, be sure to clean your bit thoroughly. This will help to prevent buildup of debris and extend the life of your bit.ConclusionTwo flute upcut CNC router bits are an excellent choice for those seeking smooth and accurate routing results. Their upcut design and optimized geometry provide clean cuts and reduced heat buildup, resulting in a polished finish. When choosing a bit, be sure to consider factors such as size, material, and flute length. By following these tips, you can maximize the life and performance of your two flute upcut CNC router bit.
High-Quality End Mills for Durable Plastic Available Now
Endmill for Plastic: Unlocking the Potential of Hard Plastic MachiningIn the world of machining, choosing the right tools can make all the difference. When it comes to working with hard plastic materials, there is a need for precision and efficiency. This is where the usage of specialized end mills for hard plastic comes into play. McMaster-Carr offers a wide range of end mills designed specifically for hard plastic machining. In this blog, we will explore the importance of using these end mills, discuss their different styles and sizes, and highlight the key benefits they bring to the table.Why Choose End Mills for Hard Plastic?Hard plastic materials such as acrylic, polycarbonate, and nylon pose unique challenges when it comes to machining. Regular end mills that are designed for working with metals may not provide optimal results in cutting, shaping, or drilling hard plastic. Using improper tools can lead to issues like melting, chipping, or even breaking of the material.This is where end mills specifically designed for hard plastic materials excel. These tools are built with specialized geometries and cutting edge designs that allow for efficient and precise machining of hard plastics. They enable clean cuts and smooth finishes without compromising the structural integrity of the plastic.Styles and Sizes for Every NeedMcMaster-Carr offers a wide selection of end mills for hard plastic, ensuring that you can find the perfect tool for your specific application. These end mills come in various styles and sizes, allowing you to cater to different machining requirements.Some common styles of end mills for hard plastic include single flute, double flute, and compression end mills. Single flute end mills work well for high-speed cutting and provide excellent chip evacuation. Double flute end mills are suitable for more intricate cutting and can handle both roughing and finishing operations. Compression end mills, on the other hand, are designed for reducing top surface burrs and work best on thin-walled materials.When it comes to sizes, McMaster-Carr offers an extensive range to suit different project needs. From small diameter end mills for detailed work to larger ones for heavy-duty operations, there is a size available for every application.Benefits of Using End Mills for Hard Plastic1. Improved Surface Finish: The specialized designs of end mills for hard plastic ensure a smoother surface finish, reducing the need for additional polishing or finishing processes.2. Reduced Material Waste: These end mills are built to efficiently cut through hard plastics, resulting in less material waste and increased productivity.3. Enhanced Tool Life: With their optimized designs, end mills for hard plastic are more resistant to wear and provide longer tool life, reducing the need for frequent tool changes.4. Precise Machining: Thanks to their geometries and cutting edge designs, these end mills allow for precise cuts, ensuring dimensional accuracy in your machined parts.5. Cost Savings: By using the right tools for the job, you can minimize material waste, improve efficiency, and reduce the need for secondary operations. This results in cost savings for your machining projects.ConclusionWhen it comes to machining hard plastics, having the right tools is essential. McMaster-Carr offers an extensive selection of end mills for hard plastic that cater to different styles, sizes, and applications. By choosing these specialized tools, you can achieve superior surface finishes, reduce material waste, enhance tool life, and ensure precise machining. So, unlock the full potential of hard plastic machining today with end mills specifically designed for the job. Trust in McMaster-Carr to provide the tools you need for successful and efficient hard plastic machining projects.
Quality End Mills for Efficient Milling Process
Milling Cutter End Mill Empowers Metalworking Industry with Efficiency and PrecisionGlobal industrial manufacturing is constantly evolving, seeking ways to optimize production processes and meet the increasing demands for efficiency and precision. Consequently, the milling cutter end mill has emerged as a game-changer in the metalworking industry, revolutionizing machining operations across various sectors. With its advanced engineering and cutting-edge technology, this innovative tool has proven indispensable for companies striving to stay ahead in the highly competitive market.Milling cutter end mill, developed by leading industry experts, represents a paradigm shift in metal cutting technology. Its outstanding design and impeccable performance have made it a go-to tool for a wide range of manufacturing applications. From aerospace to automotive, from medical to energy, this technological breakthrough has become an essential component of modern machining operations.One of the key features that sets the milling cutter end mill apart is its exceptional cutting capabilities. Equipped with specialized cutting teeth, it enables precise removal of material from a workpiece, resulting in highly accurate and intricate machined parts. The tool’s design allows for maximum cutter engagement, delivering enhanced material removal rates while minimizing vibration and chatter, ensuring optimal surface finish and dimensional accuracy.Furthermore, the milling cutter end mill boasts exceptional durability and longevity. Made from high-quality materials, such as solid carbide or high-speed steel, it offers extended tool life and enhanced reliability. This durability not only helps reduce downtime and maintenance costs but also ensures consistent performance even under high-stress conditions. Manufacturers can rely on this tool to deliver consistent results, day in and day out, enhancing overall productivity.The versatility of the milling cutter end mill is another aspect that makes it a highly sought-after tool. It comes in various shapes, sizes, and geometries, catering to the unique machining requirements of different industries. Whether it’s for roughing, finishing, or specialized operations, there is a milling cutter end mill suitable for every application. Manufacturers can choose from a wide array of options, including ball nose, corner radius, and square end mills, among others, to achieve the desired results.Moreover, the milling cutter end mill is complemented by advanced coatings and surface treatments, further amplifying its performance capabilities. These coatings, such as TiAlN, TiCN, and TiN, enhance tool life, reduce friction, and facilitate efficient chip evacuation. Such improvements help minimize heat generation, extend tool longevity, and increase cutting speeds, enabling manufacturers to achieve higher throughput and productivity levels.The introduction of the milling cutter end mill has transformed the metalworking industry, empowering manufacturers with the ability to meet the growing demands of efficiency, precision, and quality. By leveraging this technological marvel, companies can gain a competitive edge, produce complex components with ease, and maintain high standards of productivity. With its robust design, versatility, and exceptional performance, the milling cutter end mill has become an indispensable tool for industries worldwide.One company at the forefront of this technological advancement is {}. With a rich history in precision engineering and a commitment to innovation, they have spearheaded the development of state-of-the-art milling cutter end mills. Through tireless research, cutting-edge manufacturing techniques, and collaboration with industry experts, they have successfully created a range of highly efficient and reliable tools that have transformed metal cutting operations.The company prides itself on adhering to the strictest quality standards, ensuring that each milling cutter end mill delivers exceptional performance and reliability. They prioritize customer satisfaction, offering tailored solutions to meet specific machining requirements and providing ongoing support to maximize tool longevity and performance.Through partnerships with leading manufacturers and distributors worldwide, {} has made its milling cutter end mills accessible to a wide customer base, enabling companies across the globe to benefit from this groundbreaking tool. Their commitment to continuous improvement and development guarantees that they remain at the forefront of manufacturing technology, consistently delivering solutions that enable businesses to excel in their respective industries.In conclusion, the milling cutter end mill has emerged as a vital tool in the metalworking industry, driving efficiency, precision, and productivity to new heights. With its cutting-edge design, durability, versatility, and performance-enhancing coatings, it has revolutionized machining operations across various sectors. Companies like {} have played a significant role in bringing this innovative tool to the market, empowering manufacturers to meet the evolving demands of the modern industrial landscape. As the metalworking industry continues to evolve, the milling cutter end mill remains a cornerstone of progress, helping businesses thrive in an increasingly competitive global market.
Learn about the Definition of Blades in Plants and Grasses
release about the new line of high-performance blades.High-Performance Blades: The Future of Landscaping(Insert company name), a leading manufacturer of outdoor power equipment, is proud to announce their newest line of high-performance blades for lawn mowers and other landscaping equipment. These blades offer a significant upgrade from traditional blades, providing better durability, increased efficiency, and a superior cut quality.The blades are made from high-quality materials that offer unmatched strength and resilience. These materials ensure that the blades are highly resistant to wear and tear, while maintaining a sharp edge that delivers consistent performance over time. Furthermore, the innovative design and construction of these blades increase their capacity to generate more lift and suction, enhancing the efficiency of the mowing process and delivering a cleaner, more polished cut.With the new line of high-performance blades, customers are guaranteed excellent performance, whether they are mowing a small residential lawn or a large commercial property. These blades can be fitted to a range of outdoor power tools, including lawn mowers, brush cutters, and other landscaping equipment.Aside from providing outstanding performance, the blades are built to last, making them an excellent long-term investment for customers. They're not only designed to withstand heavy use, but (insert brand name) also guarantees they will last up to three times longer than traditional blades, reducing the need for frequent replacements and saving customers time and money."Over the years, we have seen a significant demand for high-performance blades amongst landscapers and homeowners alike," said (insert spokesperson name), Marketing Director at (insert company name). "So, we decided to take on the challenge of providing blades that not only offer exceptional performance but also add value to our customers' lives. We are proud to say that our new line of high-performance blades delivers on that promise."The product's launch coincides with an increasing trend towards environmentally responsible outdoor maintenance practices. Customers are demanding eco-friendly solutions that don't compromise on quality, and (insert company name)'s new line of blades is ideal for this purpose. They reduce the need for repeated mowing, and their high-performance capabilities reduce the use of fuel, making them an excellent eco-friendly option.In conclusion, (insert company name)'s new line of high-performance blades is set to revolutionize the landscaping industry. These blades offer a remarkable combination of durability and efficiency that is unmatched in the market, making them an outstanding long-term investment for customers. They are also eco-friendly, making them an excellent choice for outdoor enthusiasts who want a polished lawn without damaging the environment. Pick up a set of (insert brand name) high-performance blades today and experience the future of lawn care.