Durable and Efficient Straight Flute End Mill for Precision Machining
By:Admin
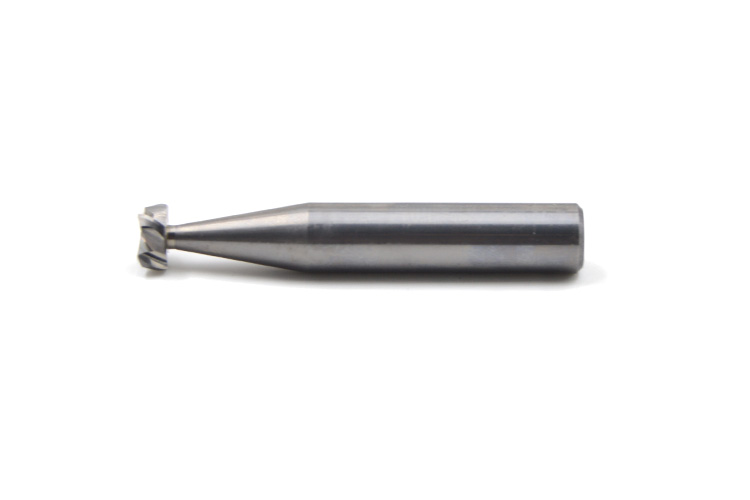
With a strong and established presence in the industry, {Company Name} has earned a reputation for producing high-quality cutting tools that meet the needs of its diverse customer base. From solid carbide end mills to drill mills and chamfer mills, the company offers a wide range of products designed to deliver precision and reliability in cutting and machining operations.
One of the key products in {Company Name}'s portfolio is the Straight Flute End Mill. This cutting tool is specifically designed to provide excellent surface finish and edge quality, making it an ideal choice for a variety of milling applications. With its straight flute design, this end mill is able to efficiently remove chips and debris from the workpiece, resulting in a smoother and more accurate machining process.
{Company Name} prides itself on the quality and performance of its cutting tools, and the Straight Flute End Mill is no exception. Manufactured to the highest standards using advanced CNC grinding and inspection equipment, this end mill offers superior precision and durability. With a range of coating options available, customers can also customize their end mills to suit specific machining requirements, whether in high-speed or high-temperature applications.
In addition to its product quality, {Company Name} also distinguishes itself with its commitment to customer service and support. The company's team of experienced engineers and technicians works closely with customers to understand their unique machining challenges and provide tailored solutions to meet their needs. This level of personalized attention has helped {Company Name} build strong and lasting relationships with its customers, earning their trust and loyalty.
As the demand for cutting tools continues to grow, {Company Name} is well-positioned to capitalize on this market opportunity. Leveraging its extensive industry experience, advanced manufacturing capabilities, and commitment to quality, the company is poised to further expand its presence in the Straight Flute End Mill market and meet the evolving needs of its customers.
In conclusion, {Company Name} is a trusted and reliable name in the cutting tools industry, and its Straight Flute End Mill is a testament to the company's dedication to providing high-quality products and exceptional customer service. With a focus on precision, performance, and customization, {Company Name} is well-prepared to meet the rising demand for cutting tools and continue its success in the market.
Company News & Blog
Discover the Key Benefits of Carbide End Mill Cutters for Enhanced Precision and Efficiency
Title: Achieving Unmatched Precision: A Breakthrough in Carbide End Mill CuttersIntroduction:In the ever-evolving realm of manufacturing and engineering, one tool has consistently stood out as a fundamental component for achieving precision: the carbide end mill cutter. Renowned for its exceptional durability and cutting performance, this tool has been a staple in various industries, ranging from aerospace and automotive to general machining and fabrication. In a groundbreaking development, a leading manufacturer in the field has unveiled a new generation of carbide end mill cutters that promise to revolutionize the industry with unmatched performance and precision.Company Background:With an illustrious history spanning decades, the company has been at the forefront of manufacturing high-quality cutting tools. Drawing on extensive research and development, their team of engineers and experts have consistently pushed the boundaries of what is possible in the field of precision machining. This commitment to innovation has earned them a reputation as a trusted provider of cutting-edge solutions that meet the evolving needs of their clients.Product Overview:The latest offering from the company is a refined iteration of the carbide end mill cutter, designed using state-of-the-art technology and cutting-edge materials. This new generation of cutters exhibits enhanced performance characteristics, making them ideal for a wide range of applications and industries.Cutting-edge Design:The team behind this revolutionary tool implemented a series of design improvements to elevate performance to unprecedented levels. To optimize cutting efficiency and precision, advanced computer simulations were employed to perfect the design of the flute geometry. The result is a more efficient chip removal process, significantly reducing heat generation and potential tool wear.Furthermore, the cutter's cutting edge has undergone optimization, enabling it to deliver precise cuts for a longer period, reducing the need for frequent tool changes and contributing to seamless production processes. This innovative design has also improved the stability and rigidity of the tool, allowing for higher machining speeds without compromising precision.Enhanced Material Composition:A key factor contributing to the exceptional performance of this carbide end mill cutter lies in the advanced material composition. The manufacturer utilizes premium carbide materials that have been meticulously engineered to provide increased hardness, toughness, and wear resistance. This ensures a cutter that can withstand the demanding conditions of high-speed machining while maintaining its cutting edge for prolonged periods, ultimately reducing downtime and increasing productivity.Versatility for Diverse Applications:Recognizing the diverse requirements of modern industries, the newly launched carbide end mill cutter is available in a range of variations, including different flute designs, coatings, and cutting edge configurations. This versatility allows manufacturers to tailor the tool to their specific needs, delivering optimal results across a variety of applications such as roughing, finishing, contouring, and profiling. From soft materials like plastics and aluminum to the toughest alloys and hardened steels, this tool is designed to excel in any machining environment.Commitment to Quality and Customer Satisfaction:The company's commitment to providing the highest quality tools is exemplified not only in its advanced manufacturing processes but also in its rigorous quality control measures. Each carbide end mill cutter undergoes stringent testing, ensuring it meets the highest industry standards and consistently delivers exceptional performance.Conclusion:With the unveiling of their latest generation carbide end mill cutter, this leading manufacturer is set to redefine precision machining. Through an innovative design and advanced material composition, the tool offers unparalleled cutting performance, extended tool life, and versatile application possibilities. As the manufacturing industry continues to evolve and demand even higher levels of precision, this revolutionary cutter sets the benchmark for excellence, setting the stage for a new era of precision machining.
High-Quality End Mills for Durable Plastic Available Now
Endmill for Plastic: Unlocking the Potential of Hard Plastic MachiningIn the world of machining, choosing the right tools can make all the difference. When it comes to working with hard plastic materials, there is a need for precision and efficiency. This is where the usage of specialized end mills for hard plastic comes into play. McMaster-Carr offers a wide range of end mills designed specifically for hard plastic machining. In this blog, we will explore the importance of using these end mills, discuss their different styles and sizes, and highlight the key benefits they bring to the table.Why Choose End Mills for Hard Plastic?Hard plastic materials such as acrylic, polycarbonate, and nylon pose unique challenges when it comes to machining. Regular end mills that are designed for working with metals may not provide optimal results in cutting, shaping, or drilling hard plastic. Using improper tools can lead to issues like melting, chipping, or even breaking of the material.This is where end mills specifically designed for hard plastic materials excel. These tools are built with specialized geometries and cutting edge designs that allow for efficient and precise machining of hard plastics. They enable clean cuts and smooth finishes without compromising the structural integrity of the plastic.Styles and Sizes for Every NeedMcMaster-Carr offers a wide selection of end mills for hard plastic, ensuring that you can find the perfect tool for your specific application. These end mills come in various styles and sizes, allowing you to cater to different machining requirements.Some common styles of end mills for hard plastic include single flute, double flute, and compression end mills. Single flute end mills work well for high-speed cutting and provide excellent chip evacuation. Double flute end mills are suitable for more intricate cutting and can handle both roughing and finishing operations. Compression end mills, on the other hand, are designed for reducing top surface burrs and work best on thin-walled materials.When it comes to sizes, McMaster-Carr offers an extensive range to suit different project needs. From small diameter end mills for detailed work to larger ones for heavy-duty operations, there is a size available for every application.Benefits of Using End Mills for Hard Plastic1. Improved Surface Finish: The specialized designs of end mills for hard plastic ensure a smoother surface finish, reducing the need for additional polishing or finishing processes.2. Reduced Material Waste: These end mills are built to efficiently cut through hard plastics, resulting in less material waste and increased productivity.3. Enhanced Tool Life: With their optimized designs, end mills for hard plastic are more resistant to wear and provide longer tool life, reducing the need for frequent tool changes.4. Precise Machining: Thanks to their geometries and cutting edge designs, these end mills allow for precise cuts, ensuring dimensional accuracy in your machined parts.5. Cost Savings: By using the right tools for the job, you can minimize material waste, improve efficiency, and reduce the need for secondary operations. This results in cost savings for your machining projects.ConclusionWhen it comes to machining hard plastics, having the right tools is essential. McMaster-Carr offers an extensive selection of end mills for hard plastic that cater to different styles, sizes, and applications. By choosing these specialized tools, you can achieve superior surface finishes, reduce material waste, enhance tool life, and ensure precise machining. So, unlock the full potential of hard plastic machining today with end mills specifically designed for the job. Trust in McMaster-Carr to provide the tools you need for successful and efficient hard plastic machining projects.
Explore the Latest Innovations in CNC Milling Machine Tools
article about the use and benefits of CNC milling machines.CNC Milling Machines: Revolutionizing Manufacturing ProcessesMilling machines have been in use for decades as tools for shaping and cutting materials into specific shapes. However, thanks to advancements in technology, modern milling machines have ushered in a new era of precision and efficiency in the manufacturing industry.One such machine is the Computer Numerical Control (CNC) milling machine. This is a type of milling machine that uses computerized controls to manage cutting tools and materials, resulting in highly precise and consistent output.With the CNC milling machine, the operator simply inputs the design specifications, and the machine takes care of the rest. From intricate designs to basic shapes, CNC machines are capable of producing highly detailed pieces with ease.One company that has made great strides in the development of CNC milling machines is [remove brand name]. With over [number of years] years of experience in the industry, [the company] has become a leading manufacturer of high-quality CNC milling machines.The Benefits of CNC Milling MachinesOne of the main benefits of CNC milling machines is the ability to produce high-quality, complex components with precision accuracy. Unlike traditional machines that require significant manual labor and expertise, CNC machines can easily produce intricate designs that would be impossible with manual milling.CNC milling machines are highly versatile and can work with a wide range of materials, including metals, plastics, and composites. This makes them ideal for manufacturing components for a variety of industries, from aerospace to automotive, medical, and more.In addition to their precision and versatility, CNC milling machines are also highly efficient. They can be programmed to perform repetitive tasks, saving manufacturers time and money in the long run. This is especially beneficial for companies that produce large volumes of components, as CNC machines can greatly reduce the time and cost required to produce each piece.CNC milling machines are also beneficial in improving the safety of manufacturing processes. With traditional milling machines, operators must manually handle materials and cutting tools, which can be dangerous and increase the risk of accidents. However, with CNC machines, the majority of the work is automated, reducing the need for manual labor and making the manufacturing process much safer for operators.The Future of CNC Milling MachinesAs technology continues to evolve, so do CNC milling machines. With advancements in automation, artificial intelligence, and other cutting-edge technologies, the possibilities for CNC milling machines are practically limitless.For example, [the company] has developed a new generation of CNC milling machines that utilize the latest technologies for improved efficiency and precision. These machines can be programmed to run multiple tasks simultaneously, allowing manufacturers to produce components faster and more accurately than ever before.As the manufacturing industry continues to evolve, CNC milling machines will undoubtedly play a critical role in shaping the way we produce components and products. With their precision, versatility, efficiency, and safety features, it's no wonder CNC milling machines have become the go-to choice for manufacturers around the world. In conclusion, CNC milling machines have revolutionized manufacturing processes by offering precision, versatility, efficiency, and safety. With the constant advancements in technology, the future of CNC milling machines looks bright and promising, and manufacturers can expect to see continued benefits from this cutting-edge technology.
Expert Guide: Unlocking the Benefits of Long Shank End Mills for Precision Machining
Long Shank End Mill: The Ultimate Tool for Precision MillingMilling is a process that involves the removal of material from a workpiece using various cutting tools. Among these tools, end mills are widely used for milling applications, especially in the manufacturing industry. Some of the types of end mills include square end, ball nose, corner radius, and long shank end mills.Long shank end mills are specialized end mills that feature extended shanks, which allows for deeper cutting depths and reach. These tools are particularly useful for milling deep cavities, slots, and pockets in materials such as steel, aluminum, and stainless steel. They are also ideal for milling hard materials, such as hardened steels and tool steels.One of the leading manufacturers of long shank end mills is a company that has been providing innovative cutting solutions since 1969. Specializing in the design and production of high-performance carbide cutting tools for the aerospace, automotive, and medical industries, the company has made a name for itself as a trusted and reliable source of cutting-edge tools.The company's long shank end mills are designed to provide optimal performance and longevity, even in the most demanding applications. These tools are made from premium grade carbide materials, which offer high hardness, wear resistance, and toughness. The company also uses advanced manufacturing techniques to produce precise cutting edges, which ensures accurate and consistent results.One of the key advantages of the company's long shank end mills is their extended reach capability. With shank lengths ranging from 4 inches to 8 inches, these tools can reach deep areas that other end mills cannot reach. This allows for increased productivity, less downtime, and reduced tool changeovers, which ultimately translates into cost savings for the user.Another important feature of the company's long shank end mills is their optimized flute design. The flutes are designed to remove chips efficiently and quickly, which prevents heat buildup and prolongs tool life. Additionally, the company offers a wide range of flute geometries, such as variable helix and variable pitch, to meet the specific needs of different applications.The company also provides customization services for its long shank end mills. Customers can specify the shank length, overall length, flute length, and other parameters to suit their unique requirements. The company's engineering team works closely with customers to develop customized solutions that meet their exacting specifications.In addition to long shank end mills, the company offers a wide range of cutting tools, including drills, reamers, countersinks, and thread mills. All of these tools are made from high-performance carbide materials and feature advanced designs for optimal performance and longevity.The company's commitment to quality is evident in its ISO 9001:2015 certification, which ensures that its products meet rigorous quality standards. Additionally, the company's state-of-the-art manufacturing facility utilizes the latest technologies, such as 5-axis CNC grinding machines, to ensure accurate and precise cutting tool production.Overall, the company's long shank end mills are an essential tool for precision milling applications that require deep cutting depths and extended reach. With their superior performance, durability, and customization options, these tools offer a competitive advantage to manufacturers across a wide range of industries.
Unprecedented Drilling Operation Successfully Completed in the Arctic
Title: Groundbreaking Innovation in Power Drilling Technology Revolutionizes Construction IndustryIntroduction:In a groundbreaking development for the construction industry, a leading company specialized in manufacturing power tools has unveiled its latest innovation in power drilling technology. The new product, known as Center Drill, promises to revolutionize the way construction professionals approach drilling projects. With an advanced design and cutting-edge features, Center Drill is set to become a game-changer, ensuring increased efficiency, improved accuracy, and enhanced safety.I. Background:(Company Name), a renowned name in the power tool industry, has a history of delivering innovative solutions to meet the evolving needs of professionals in various sectors. With its tireless commitment to research and development, the company has continually pushed boundaries to provide cutting-edge tools. The launch of Center Drill marks yet another milestone in their mission to empower construction industry professionals.II. The All-New Center Drill:1. Advanced Design and Technology:Center Drill boasts a sleek and ergonomic design that maximizes user comfort, reducing fatigue during extended drilling operations. The tool's lightweight construction does not compromise its robustness, making it suitable for various construction applications. Furthermore, Center Drill features a high-powered motor that ensures reliable performance and long service life.2. Enhanced Efficiency:The innovative drill offers exceptional drilling speed, enabling users to complete projects in record time. With its superior torque control system, Center Drill ensures efficient power transfer, effectively reducing the drilling time required for each hole. Its precise depth control mechanism also guarantees accurate drilling, minimizing errors and maximizing productivity.3. Improved Accuracy and Safety:Center Drill impresses with its intelligent electronic control system, which includes advanced sensors to maintain optimal drilling conditions. The system constantly monitors the drilling process, preventing overheating, overloading, and potential damage. This feature not only extends the lifespan of the tool but also enhances safety for the operators and surrounding personnel.4. Versatility:Equipped with interchangeable drill bits of various sizes, Center Drill caters to a wide range of drilling applications, from simple household projects to extensive commercial constructions. This versatility ensures that professionals can rely on a single device for multiple tasks, eliminating the need for investing in different tools.III. Benefits for the Construction Industry:1. Increased productivity:The exceptional speed and efficiency of Center Drill significantly accelerate drilling operations, enabling professionals to complete projects within strict deadlines. The reduced drilling time translates into increased productivity, saving valuable time and resources for construction companies.2. Cost-effectiveness:By offering versatility and precision drilling, Center Drill reduces the chances of errors and rework. This not only saves construction professionals additional expenses but also enhances overall project profitability.3. Enhanced Safety:Center Drill incorporates several safety features that prioritize the well-being of operators and those working in close proximity. The device's intelligent electronic control system and advanced sensors protect against potential hazards, minimizing risks and accidents.IV. Industry Demand and Reception:The introduction of Center Drill has generated significant excitement within the construction industry. Experts are praising the tool's advanced features, as they cater to the evolving needs of professionals seeking efficiency, accuracy, and safety. Early reviews from pilot users suggest that Center Drill has already surpassed expectations and is poised to become a trusted and indispensable tool for construction projects of all scales.Conclusion:Center Drill, with its innovative design, advanced technology, and focus on efficiency and safety, promises to disrupt the construction industry's approach to drilling. With its potential to increase productivity, reduce costs, and improve precision, Center Drill has catapulted (Company Name) to the forefront of power tool manufacturers. As construction professionals embrace this groundbreaking drilling technology, it becomes evident that Center Drill is set to shape the future of the industry.
Exploring the Versatility and Benefits of Flute Drills in the News
Title: Innovative Flute Drills Revolutionize the Manufacturing IndustryIntroduction:In today's rapidly advancing world of manufacturing, companies are constantly on the lookout for innovative tools and equipment that can streamline their operations and enhance productivity. The introduction of Flute Drills by a leading company is a prime example of how cutting-edge technology is changing the game for manufacturers across the globe. These revolutionary tools are poised to transform the way drilling is done, offering unparalleled efficiency and precision. This article explores the features and benefits of Flute Drills and their potential impact on the manufacturing industry.1. The Evolution of Flute Drills:Flute Drills have evolved significantly over the years, thanks to advancements in engineering and cutting-edge materials used in their construction. Traditional drills often struggled with chip evacuation and excessive heat buildup, limiting their effectiveness and causing damage to workpieces. However, Flute Drills incorporate innovative technology that addresses these challenges, making them an indispensable tool for manufacturers.2. Unparalleled Performance:These new age Flute Drills feature a unique flute design that allows for efficient chip evacuation, reducing the risk of clogging and enhancing productivity. The drills are engineered to deliver improved stability, reducing the likelihood of tool vibration and improving accuracy. With their superior heat resistance capabilities, these drills can handle higher cutting speeds, extending tool life and minimizing downtime.3. Enhanced Durability:Manufacturers are always seeking ways to increase the lifespan of their tools, as frequent replacements not only incur additional costs but also impact productivity. Flute Drills are constructed using advanced materials that offer exceptional durability, ensuring prolonged usage and enhanced performance. Manufacturers can rely on these drills to withstand high-speed machining and deliver consistent results for extended periods, significantly reducing the need for replacements.4. Wide Range of Applications:Flute Drills are versatile tools that find application in various industries, such as aerospace, automotive, and general manufacturing. Their ability to handle multiple materials, including metals, composites, and alloys, makes them invaluable for manufacturers working on diverse projects. Whether it is drilling precision holes or expanding existing ones, Flute Drills cater to a wide range of requirements, making them an essential tool in the manufacturing process.5. Cost Savings and Increased Efficiency:Utilizing Flute Drills can result in substantial cost savings for manufacturers. The enhanced chip evacuation and heat resistance properties translate into reduced downtime, increased productivity, and improved tool life. Manufacturers can achieve higher machining speeds without compromising on accuracy, meeting project deadlines efficiently. These drills also minimize the need for additional tooling, reducing overall costs and enhancing operational efficiency.6. Environmental Benefits:In addition to the economic advantages, Flute Drills also have a positive impact on the environment. Improved chip evacuation and reduced heat buildup mean fewer resources are wasted, making the manufacturing process more sustainable. By reducing tool replacements and minimizing energy consumption, these drills contribute to a greener and more environmentally responsible manufacturing industry.Conclusion:As manufacturing industries continue to evolve and embrace cutting-edge technologies, Flute Drills represent a pivotal development in the field of drilling tools. Their superior performance, enhanced durability, and wide range of applications make them a go-to solution for manufacturers worldwide. The incorporation of Flute Drills enables companies to optimize production processes, reduce costs, and increase overall efficiency. Embracing this innovative technology will undoubtedly propel the manufacturing industry to new heights of success.
CNC Machines Can Now Benefit from Micro Diameter End Mills
Title: Revolutionary Micro Diameter End Mill Enhances Precision in CNC MachiningIntroduction:Innovation and precision are two pillars of growth for the manufacturing industry. Enhancing these attributes, a renowned cutting tool manufacturer has recently introduced a breakthrough product - the Micro Diameter End Mill for CNC machines. Pioneering the field of micro machining, this cutting-edge tool promises unparalleled precision and improved performance, revolutionizing the world of CNC machining.Body:1. Background and Introduction to Micro Diameter End Mill:CNC (Computer Numerical Control) machining has long been the gold standard for producing high-precision parts. However, the ever-increasing demand for smaller and more intricate components has led to the development of specialized tools. The Micro Diameter End Mill is engineered to meet these evolving demands, offering remarkable precision and improved surface finish.2. Unmatched Precision and Surface Finish:Utilizing advanced manufacturing techniques and the highest quality materials, the Micro Diameter End Mill delivers unparalleled precision in micro machining applications. With a diameter range of less than 1mm, this innovative tool optimizes small-scale operations, facilitating the production of intricate details with utmost accuracy. Its ultra-sharp cutting edges minimize deviations, leading to a superior surface finish and reducing the need for post-machining operations.3. Enhanced Durability and Longevity:The company behind this revolutionary tool has invested substantial resources in R&D to develop a durable and long-lasting end mill. By leveraging cutting-edge materials and heat treatment processes, the Micro Diameter End Mill exhibits exceptional wear resistance and extended tool life. This ensures consistent performance over prolonged operations, reducing downtime and replacement costs for manufacturers.4. Versatile Applications:The Micro Diameter End Mill finds applications across various industries, including aerospace, medical devices, electronics, and precision engineering. Its ability to produce intricate components with unmatched accuracy makes it ideal for manufacturing micro parts used in miniaturized electronic devices, surgical instruments, and aerospace components, among others. This versatile end mill can effectively handle materials ranging from soft metals like aluminum to tough alloys like titanium.5. Advanced Coating Technology:To further enhance performance, the tool is coated with an advanced wear-resistant material. This coating not only increases the tool's durability but also reduces friction during machining, resulting in improved chip evacuation and reduced cutting forces. Consequently, manufacturers can achieve higher speeds and feeds without compromising the tool's integrity.6. Commitment to Sustainability:In line with global concerns about environmental sustainability, the company has also prioritized the development of eco-friendly processes in manufacturing the Micro Diameter End Mill. Emphasizing responsible sourcing and reducing waste, the tool is manufactured using eco-friendly materials and sustainable manufacturing techniques.7. Customer-Centric Approach:The company's dedication to customer satisfaction is reflected in the ongoing partnership and support they provide. The development of the Micro Diameter End Mill incorporates valuable insights and feedback gathered from a wide-ranging collaboration with industry experts and machine operators. By closely working with end-users, the tool's design has been optimized to exceed expectations, further establishing it as an industry leader.Conclusion:As the manufacturing industry increasingly demands higher precision and accuracy, the introduction of the Micro Diameter End Mill represents a significant step forward in CNC machining. With its unparalleled precision, advanced coating technology, and commitment to sustainability, this groundbreaking tool is set to redefine the possibilities of micro machining. Providing manufacturers with the means to create complex and intricate components, the Micro Diameter End Mill is poised to revolutionize the world of CNC machining.
Get Better Results with Indexable End Mills for Precision Machining
Indexable End Mill Tools Revolutionize Manufacturing ProcessesIndexable end mill tools have been making waves in various industries since their inception. Used primarily by manufacturing and production companies, these tools have been gradually gaining popularity due to their cost-effectiveness and durability. In the past, companies that relied heavily on milling machines needed to replace their costly solid carbide end mills frequently. With the introduction of indexable end mill tools, this is no longer the case.One of the most significant advantages of indexable end mill tools is that their cutting edges can be replaced. This results in significant cost savings, as users do not need to replace the entire tool when the cutting edges become dull. Rather, they can replace the damaged or broken cutting edges with a new one, resulting in cost savings of up to 60% compared to solid carbide end mills.Furthermore, indexable end mill tools provide improved cutting edge quality due to the use of high-quality coatings. The coatings provide added durability, and the cutting edges maintain their sharpness and performance even when working on tough materials. This results in higher cutting speeds and feeds, leading to increased productivity.Another advantage of indexable end mill tools is their versatility. These tools can be used in a wide range of applications, ranging from roughing to finishing operations. Additionally, users can easily interchange the cutting edges without having to disassemble the tool from the tool holder, thus saving time and effort.The company (name removed) has been at the forefront of manufacturing indexable end mill tools. With over 25 years of experience in tool manufacturing, the company has developed a range of high-quality indexable end mill tools for various applications. Their tools are designed to offer maximum productivity, reduced cycle times, and enhanced precision.The company uses state-of-the-art manufacturing techniques and technology to produce indexable end mill tools that are durable and efficient. They also offer customized solutions to meet the specific needs of different industries. Some of the industries that have benefitted from their tools include aerospace, automotive, medical, and energy.One of the unique features of the company's indexable end mill tool is its double-side pocket design. This design allows for more cutting edges, resulting in increased productivity and cost savings. Additionally, their tools are designed to provide higher rigidity and improved surface finish, reducing the need for further machining operations.The company takes pride in its commitment to quality and innovation. Their tools undergo stringent quality control tests to ensure that they meet the highest standards. They also invest heavily in research and development to continuously improve their products and stay ahead of the competition.In conclusion, indexable end mill tools offer a cost-effective and efficient alternative to solid carbide end mills. Companies can benefit significantly from the cost savings, improved cutting edge quality, and versatility of these tools. With the introduction of innovative designs and manufacturing techniques, companies like (name removed) are leading the way in providing high-quality indexable end mill tools for various industries.
Creative Paper Cut Art Ideas - Inspiring Cuttings for Your Next Project
, paper cutting, paper cut art, and paper art.Paper Cutting: An Art Form That Continues to Captivate the WorldPaper cutting is a form of art that has been around for many years. It involves cutting paper into different shapes and patterns to create unique pieces of art. Paper cutting has been used for a variety of purposes, including decoration, illustration, and even as templates for embroidery and textiles. This art form continues to captivate the world, with people creating intricate designs that are truly breathtaking.One of the tools used for paper cutting is the T Cutter. This tool is designed to cut paper in a straight line, allowing artists to create precise cuts. The T Cutter is an essential tool for any paper cutting artist, as it helps them to create clean and accurate cuts.Paper cutting has many benefits, both artistic and therapeutic. For many artists, it is a form of expression that allows them to create beautiful pieces of art that can be shared with the world. Paper cutting can be done by anyone, regardless of skill level, making it a great hobby for people of all ages. It is also a great way to relax, relieve stress, and clear the mind.Paper cut art is another aspect of paper cutting that continues to gain popularity. This art form involves creating intricate designs using multiple layers of paper, often resulting in a three-dimensional piece of art. Paper cut art is truly remarkable, with artists creating stunning works of art that are both beautiful and impressive.Paper art is another form of paper cutting that is gaining popularity. This art form involves using paper to create sculptures, installations, and even furniture. Paper art is a unique form of art that is both beautiful and eco-friendly.In conclusion, paper cutting is an art form that continues to captivate the world. With the use of tools like the T Cutter, artists can create intricate designs that are truly breathtaking. Whether creating paper cut art or paper art, paper cutting is a therapeutic and artistic outlet that can be enjoyed by anyone regardless of their skill level.