Get Better Results with Indexable End Mills for Precision Machining
By:Admin
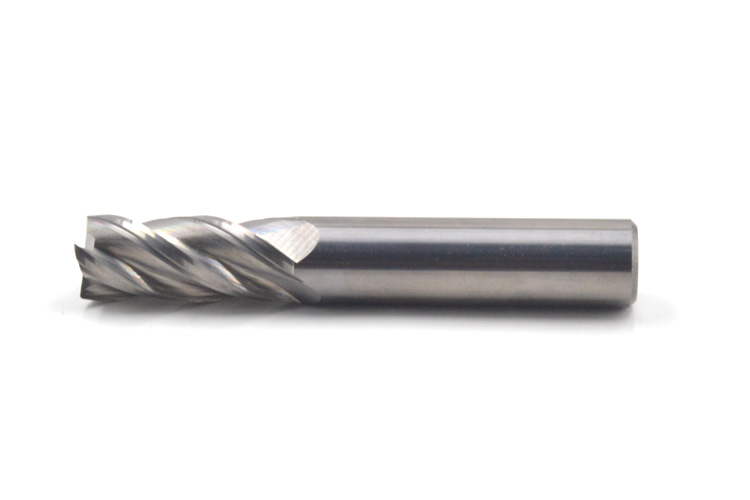
Indexable end mill tools have been making waves in various industries since their inception. Used primarily by manufacturing and production companies, these tools have been gradually gaining popularity due to their cost-effectiveness and durability. In the past, companies that relied heavily on milling machines needed to replace their costly solid carbide end mills frequently. With the introduction of indexable end mill tools, this is no longer the case.
One of the most significant advantages of indexable end mill tools is that their cutting edges can be replaced. This results in significant cost savings, as users do not need to replace the entire tool when the cutting edges become dull. Rather, they can replace the damaged or broken cutting edges with a new one, resulting in cost savings of up to 60% compared to solid carbide end mills.
Furthermore, indexable end mill tools provide improved cutting edge quality due to the use of high-quality coatings. The coatings provide added durability, and the cutting edges maintain their sharpness and performance even when working on tough materials. This results in higher cutting speeds and feeds, leading to increased productivity.
Another advantage of indexable end mill tools is their versatility. These tools can be used in a wide range of applications, ranging from roughing to finishing operations. Additionally, users can easily interchange the cutting edges without having to disassemble the tool from the tool holder, thus saving time and effort.
The company (name removed) has been at the forefront of manufacturing indexable end mill tools. With over 25 years of experience in tool manufacturing, the company has developed a range of high-quality indexable end mill tools for various applications. Their tools are designed to offer maximum productivity, reduced cycle times, and enhanced precision.
The company uses state-of-the-art manufacturing techniques and technology to produce indexable end mill tools that are durable and efficient. They also offer customized solutions to meet the specific needs of different industries. Some of the industries that have benefitted from their tools include aerospace, automotive, medical, and energy.
One of the unique features of the company's indexable end mill tool is its double-side pocket design. This design allows for more cutting edges, resulting in increased productivity and cost savings. Additionally, their tools are designed to provide higher rigidity and improved surface finish, reducing the need for further machining operations.
The company takes pride in its commitment to quality and innovation. Their tools undergo stringent quality control tests to ensure that they meet the highest standards. They also invest heavily in research and development to continuously improve their products and stay ahead of the competition.
In conclusion, indexable end mill tools offer a cost-effective and efficient alternative to solid carbide end mills. Companies can benefit significantly from the cost savings, improved cutting edge quality, and versatility of these tools. With the introduction of innovative designs and manufacturing techniques, companies like (name removed) are leading the way in providing high-quality indexable end mill tools for various industries.
Company News & Blog
What is a Rotary Tool-Steel Cutter Used in Milling Machines?
Metal Milling Cutter: An OverviewEvery manufacturing process involves various cutting tools and machines. Among the most commonly used tools in the industry is the milling cutter. A milling cutter is a cutting tool used in a milling machine that is designed to shape, cut, and dress metal surfaces. In this blog, we'll cover the basics of milling cutters, their types, and applications.What is a Milling Cutter?A milling cutter is a rotating cutting tool that is mounted on a milling machine spindle. It is designed to remove material from a workpiece by advancing or rotating the cutter into the workpiece. The material removal process is achieved through the cutting edges on the milling cutter. These edges can be a combination of lips, flutes, teeth, or other features.Milling cutters come in various shapes and sizes and are made of different materials, including high-speed steel, cobalt, carbide, and diamond-coated. These cutters are selected based on the type of material to be machined and the desired surface finish.Types of Milling CuttersThere are many different types of milling cutters available in the industry. Here are some of the most popular ones:1. End MillEnd mills are among the most commonly used milling cutters. They are designed for cutting slots, profiling, and contouring. End mills come in a variety of shapes and sizes, such as square, ballnose, and corner radius.2. Face MillFace mills are designed to machine flat surfaces, and they have a large surface area compared to other milling cutters. The cutting edges are located on the face of the mill, and they produce a flat finish.3. Ball Nose CutterBall nose cutters are designed for producing rounded contours in a workpiece. They have a hemispherical shape with two cutting edges.4. T-slot CutterT-slot cutters are used for milling slots with a T-shaped profile. They have a straight shank with a T-shaped cutting edge.Applications of Milling CuttersMilling cutters are used in various applications, including:1. Machining complex shapesMilling cutters are often used to machine complex shapes that would be difficult or impossible to achieve with other cutting tools.2. High-precision machiningMilling cutters are capable of producing high-precision finishes on workpieces. They can be used to achieve tight tolerances on machined surfaces.3. Mass productionMilling cutters can be used in mass production processes to machine large quantities of parts. They are efficient and produce consistent results.ConclusionMilling cutters are essential cutting tools in the manufacturing process. They are designed to shape, cut, and dress metal surfaces with precision and efficiency. There are various types of milling cutters, including end mills, face mills, ball nose cutters, and T-slot cutters, each with unique features and applications. Selecting the right milling cutter for the job is crucial to achieve the desired surface finish and efficiency in the machining process.
Boost Your Machining Efficiency with a Top-Quality Thread Mill Cutter
Thread Mill Cutter Company leads the way in innovative and customized solutions for cutting-edge milling technologies. Founded in the early 2000s, this dynamic company has revolutionized the industry by developing cutting-edge algorithms to produce superior quality thread milling cutters.The Thread Mill Cutter Company is a recognized global leader in developing and manufacturing utility-grade thread milling cutters. With factories established in various parts of the world, the company's products are widely used across various industries such as automotive, aerospace, medical equipment, and machinery. The company's long-standing professionalism and commitment to quality have earned them an industry-leading reputation for producing top-of-the-line products.The cutting-edge technology that Thread Mill Cutter Company uses, utilizes the latest advances in material engineering to create an ultra-modern and sophisticated design. The cutting-edge algorithms and computational techniques used by the team are unparalleled in the industry, and have set Thread Mill Cutter Company Apart from their competition. The company's modern and efficient factories allow them to delivery high-quality products that meet or exceed the stringent international quality standards, required for various industries.Thread Mill Cutter's products are designed with the utmost precision, down to individual nanometers which give them a competitive edge in the market. The product range is extensive and versatile, ranging from standard thread milling cutters, specialized cutters, multi-flute cutters, and much more. This impressive product line offers tailor-made solutions that guarantee greater efficiency and productivity for industries worldwide.The Thread Mill Cutter Company is known for their impeccable customer service which is centered on a customer-centric approach. Their cutting-edge solutions are designed around catering to the individual needs of each and every one of their clients. The company's team of experts examines each customer's requirements carefully and makes custom solutions to fit their exact needs.The company’s philosophy of innovation and cutting-edge research and development has led the industry to rely on Thread Mill Cutter for their state-of-the-art technology. The research and Development department at Thread Mill Cutter is comprised of a team of passionate experts in mathematics, physics, and mechanical engineering. All of the team's skilful research and development efforts are embodied in the extensive line of products offered by the Thread Mill Cutter Company and their new innovative solutions.The Thread Mill Cutter Company has always been committed to being a socially responsible company. They are taking firm steps to protect the environment through using sustainable development patterns, such as improving manufacturing processes, reducing unnecessary waste, and using environmentally friendly material. Future plans to invest in green electricity will see the company help fight climate change and the carbon footprint left by traditional energy sources.In conclusion, the Thread Mill Cutter Company's world-class state-of-the-art technology, the focus on customer support, and pursuit of environmentally friendly solutions are reasons why the company is leading the milling technology industry. With their dedication to quality, exceptional customer service, and commitment to green solutions for the world, it's no wonder they have become a go-to tech solution for businesses worldwide. The Thread Mill Cutter Company is expected to continue its growth in the industry to become one of the most influential companies worldwide.
High-Performance Indexable Carbide Insert T-Slot Milling Cutter for Various Bolt Sizes - ID 1099
Title: Unveiling the Power of Indexable Carbide Insert T-Slot Cutters: The Game Changer for Precision T-Slot MillingIntroduction (approx. 80 words)Indexable carbide insert T-slot cutters have revolutionized the machining industry with their unique design and unrivaled performance. In this blog post, we will delve into the world of T-slot cutting and explore why these cutters are a game changer for precision milling. With a special focus on the 1/2', 5/8', and other popular sizes, we will uncover the secrets behind these tools and shed light on why carbide T-slot cutters are the preferred choice in the market today.1. What is a Carbide T-Slot Cutter? (approx. 150 words)Before we dive deeper, let's understand what exactly a carbide T-slot cutter is. A T-slot cutter is a specialized milling tool used to create T-slots or T-grooves on workpieces. These slots are essential for securely fastening bolts and fixtures to the workpiece, commonly found in the automotive, machinery, and aerospace industries.Carbide T-slot cutters, as the name suggests, are made of carbide inserts, a material known for its strength, durability, and excellent heat resistance. The combination of indexable carbide inserts and a unique design not only provides exceptional cutting performance but also allows for easy tool replacement and increased cost-effectiveness.2. Features and Benefits of Indexable Carbide Insert T-Slot Cutters (approx. 300 words)a) Superior Cutting Performance: Carbide T-slot cutters excel in high-speed machining operations due to their exceptional hardness and heat resistance. The indexable inserts are designed to ensure fast and accurate cutting, resulting in clean and precise T-slots.b) Versatility in Application: These T-slot cutters cater to a wide range of workpiece sizes. With options available for 1/2 inch, 5/8 inch, 3/4 inch, 1 inch, 1-1/4 inch, and 1-1/2 inch bolt sizes, they provide flexibility and adaptability to various machining projects.c) Cost-effectiveness: The indexable nature of these cutters allows for easy tool replacement, eliminating the need for resharpening or discarding the entire cutter. By replacing only the inserts, machining costs are significantly reduced in the long run.d) Enhanced Tool Life: Carbide inserts are known for their extended tool life compared to traditional high-speed steel cutters. The advanced wear resistance and durability of carbide inserts help maintain sharp cutting edges for prolonged periods, ensuring consistent performance over time.e) Minimal Downtime: With simple insert replacement, downtime for tool changes is minimized, leading to increased productivity. This quick and easy process saves valuable machining time, allowing for uninterrupted workflow and reduced operational costs.3. Unlocking Precision Milling with Carbide T-Slot Cutters (approx. 250 words)Precision milling requires accuracy, reliability, and consistency. Carbide T-slot cutters are designed to meet these stringent requirements, enabling machinists to achieve exceptional results. Whether it be creating precise T-slots for fixturing or producing intricate grooves on various workpiece materials, these cutters offer unprecedented precision.Additionally, the unique design of these cutters enables smooth chip evacuation, reducing the risk of tool wear and workpiece damage. The carefully engineered geometry of the T-slot cutter ensures efficient material removal while minimizing heat generation, resulting in longer tool life and enhanced productivity.4. The Significance of Carbide T-Slot Cutters in the Machining Industry (approx. 220 words)The machining industry is constantly evolving, demanding tools that can keep up with the growing complexities. Carbide T-slot cutters have emerged as a popular choice due to their exceptional quality and unmatched performance.Their prowess in creating precise and sturdy T-slots has propelled these cutters to the forefront of machining technology, earning them a reputation as reliable and efficient tools. Manufacturers and machinists worldwide rely on them for various applications, from milling complex components to producing flawless T-slots.The market demand for T-slot cutters has surged due to the growing need for versatility, accuracy, and cost-effectiveness in machining operations. Carbide T-slot cutters offer all these benefits and more, making them an invaluable asset for any modern workshop or manufacturing facility.Conclusion (approx. 100 words)Indexable carbide insert T-slot cutters have revolutionized precision milling, with their unparalleled cutting performance and durability. With the ability to create clean and precise T-slots, these cutters have become a staple in the machining industry. Offering versatility, cost-effectiveness, and extended tool life, carbide T-slot cutters have proven to be invaluable tools for achieving precision and efficiency in various machining applications.
Premium Carbide spot drill with TiALN coating and 2 flutes, 120 degree angle and 1-1/4" flute length
When it comes to making precision holes in metal, having the right tools is essential. And one tool that every machinist should have in their arsenal is a high-quality spot drill. A spot drill is a type of drill bit that's designed to create a small indentation in the surface of the metal before drilling through it. This indentation helps to guide the drill bit and ensures that the hole is perfectly centered and the right size. And when it comes to spot drills, the 1/2" 2 Flute 120 Degree Carbide Spot Drill with a TiALN Coating is one of the best options available on the market today.One of the key features of the 1/2" 2 Flute 120 Degree Carbide Spot Drill is its TiALN coating. This coating is a type of hard, wear-resistant material that's applied to the surface of the drill bit using a process called physical vapor deposition (PVD). The TiALN coating helps to extend the life of the drill bit by reducing friction and heat buildup during use. This, in turn, helps to prevent the drill bit from overheating or becoming dull, which can result in a poor-quality hole.Another advantage of the 1/2" 2 Flute 120 Degree Carbide Spot Drill is its 10% cobalt micrograin material. This is a type of high-speed steel that's made using a special process that results in a more uniform grain structure. This, in turn, makes the material stronger and more wear-resistant than standard high-speed steel. The 10% cobalt micrograin material is especially well-suited for use in CNC grinders, where precision and consistency are essential.One final feature of the 1/2" 2 Flute 120 Degree Carbide Spot Drill is its 1-1/4" flute length. This length is perfect for creating deep holes in metal without the need for frequent repositioning of the drill bit. It also helps to prevent the drill bit from breaking or bending, which can happen when drilling through thick or hard materials.Overall, the 1/2" 2 Flute 120 Degree Carbide Spot Drill with a TiALN Coating is an excellent choice for anyone who needs to create precision holes in metal. Its TiALN coating, 10% cobalt micrograin material, and 1-1/4" flute length all contribute to its exceptional performance and durability. So if you're in the market for a new spot drill, be sure to check out this high-quality option.
Top Cutting Tools for Sewing: A Guide to Choosing the Best Tools for Your Projects
Cutting Tools: The Backbone of the World of SewingCutting tools are an essential element of every sewing project, and they form the backbone of the entire sewing industry. When it comes to effective and efficient cutting tools, BERNINA World of Sewing emerges as one of the leading contenders in the market. But beyond the popular brand name, there is much more to explore about cutting tools that make the job of sewing a lot easier.Special Cutting ToolsWhile scissors and rotary cutters are well-known cutting tools, it is essential to note that there are more special cutting tools available out there. These cutting tools are specifically designed to cut different types of fabrics and materials, and they come in handy in different situations. These special cutting tools include:1. Electric Fabric Cutters - These cutters are powered by electricity, and they are known for their precision and speed. They are specially designed to cut through layers of fabrics, making them ideal for quilting and bulk cutting. They are easy to use, and they come with different blade options.2. Pinking Shears - These pair of scissors feature zigzag blades, which produce a zigzag edge while cutting. They are ideal for creating a decorative edge, and they prevent fabric fraying. Pinking shears are a great option for finishing seams, hemming, and creating a decorative edge.3. Fabric Scissors - These are also known as dressmaker scissors, and they are designed to cut through different types of fabrics. They have long blades that make it easy to cut through fabric in a straight line, and they are perfect for dressmaking, tailoring, and upholstery.4. Thread Clippers - These are small scissors that are perfect for cutting threads and light fabrics. They are ideal for cutting embroidery threads, stabilizers, and lightweight fabrics. They are lightweight and easy to handle, making them ideal for precision cutting.5. Seam Rippers - These are special tools used for removing stitches. They have a pointed end that helps to cut through stitches, and they are ideal for ripping out unwanted stitches without damaging the fabric.All these special cutting tools make the job of sewing a lot easier. The efficiency and precision they bring to the table make them a must-have in every sewing toolkit. They are easy to use, and they come in handy in different situations.Cutting Tools by BERNINA World of SewingBERNINA World of Sewing is a popular brand known for producing high-quality sewing machines and accessories. They also produce different cutting tools that are renowned for their precision and efficiency. Some of their well-known cutting tools include:1. BERNINA Rotary Cutters - These rotary cutters are known for their precision and ease of use. They cut through multiple layers of fabrics with ease, making them ideal for quilting and bulk cutting. They come with different blade options, making them perfect for different types of fabrics.2. BERNINA Scissors - These scissors are specially designed to cut through different types of fabrics. They have long blades that make it easy to cut through the fabric in a straight line, and they come in different sizes and shapes. They are perfect for dressmaking, tailoring, and upholstery.3. BERNINA Seam Rippers - These seam rippers are efficient in removing stitches without damaging the fabric. They have a pointed end that glides readily through stitches, making it easy to remove unwanted stitches.4. BERNINA Electric Fabric Cutters - These cutters are known for their speed and precision. They are designed to cut through multiple layers of fabrics, and they come with different blade options.These cutting tools are essential in the world of sewing, and BERNINA World of Sewing provides exceptional quality and precision that makes sewing a lot easier.ConclusionIn conclusion, cutting tools are the backbone of the world of sewing. Special cutting tools make sewing a lot easier, as they provide precision and efficiency in different situations. BERNINA World of Sewing provides high-quality and exceptional cutting tools that speak of the brand's commitment to excellence and customer satisfaction. Whether you are a beginner or an experienced seamstress, investing in good quality cutting tools is a must. They make sewing a lot easier, and the precision they provide is unmatched.
Precision Solid Carbide Drills: High-Quality Tools for Optimal Performance
[News Title]Solid Carbide Drills: A High-Performance Solution for Precision Drilling Needs[News Introduction]Solid Carbide Drills, manufactured by a renowned industry leader, are gaining widespread popularity among professionals in various sectors due to their exceptional performance and durability. These cutting-edge tools have revolutionized precision drilling by offering superior quality, extended tool life, and increased productivity. Designed to meet the ever-growing demands of modern drilling operations, Solid Carbide Drills are becoming the go-to option for professionals seeking a reliable and efficient drilling solution.[Company Introduction]With a rich history of more than [number] years in the manufacturing industry, Company X has established itself as a market leader known for producing cutting-edge tools. Known for their commitment to quality and innovation, Company X has invested heavily in research and development to create products that meet the evolving needs of professionals in various industries.[Body - Paragraph 1]Solid Carbide Drills, developed by Company X, are engineered from high-grade carbide material that offers exceptional hardness and resistance to wear. This advanced material composition enables these drills to endure extreme drilling conditions without compromising on performance and precision. Built to last, Solid Carbide Drills have gained a reputation for their longevity, resulting in reduced downtime and increased cost-efficiency for users.[Body - Paragraph 2]One of the key features of Solid Carbide Drills is their superior cutting ability. Equipped with sharp cutting edges, these drills effortlessly penetrate through various materials, including steel, stainless steel, cast iron, and non-ferrous alloys. This versatility makes Solid Carbide Drills a preferred choice for professionals working in industries such as automotive, aerospace, energy, and general manufacturing, where precision drilling is a critical requirement.[Body - Paragraph 3]The design of Solid Carbide Drills incorporates innovative chip flute geometries, which are instrumental in efficiently evacuating chips from the drilled hole. This feature effectively prevents chip accumulation and subsequent tool clogging, ensuring uninterrupted drilling and improved hole quality. Moreover, the flute design also contributes to reduced cutting forces, enabling smoother drilling operations and lower power consumption.[Body - Paragraph 4]To enhance user convenience and adaptability, Solid Carbide Drills offered by Company X are available in various sizes and configurations, catering to a wide range of drilling requirements. Whether it's a shallow or deep hole, small or large diameter, or even complex hole geometries, professionals can find a suitable Solid Carbide Drill to achieve precise and accurate drilling results.[Body - Paragraph 5]Apart from their outstanding performance, Solid Carbide Drills are also known for their environmental friendliness. The carbide material used in their construction is recyclable, allowing for a more sustainable drilling solution. Company X actively promotes responsible manufacturing practices, further showcasing their commitment to sustainability and the environment.[Body - Paragraph 6]Company X's dedication to customer satisfaction extends beyond their product quality. They provide comprehensive technical support and guidance to users, ensuring that professionals make the most of their Solid Carbide Drills. Their team of industry experts is readily available to address any queries or concerns, offering valuable assistance and expertise to enhance drilling processes.[Conclusion]Solid Carbide Drills, developed and manufactured by Company X, have revolutionized the drilling industry with their superior performance, durability, and precision. As professionals across various sectors seek high-quality drilling solutions, Solid Carbide Drills have emerged as the go-to choice, offering unmatched reliability and efficiency. With their innovative design and commitment to sustainability, Company X continues to lead the way in providing cutting-edge tools that meet the evolving needs of modern drilling operations.
High-Quality End Mills for Durable Plastic Available Now
Endmill for Plastic: Unlocking the Potential of Hard Plastic MachiningIn the world of machining, choosing the right tools can make all the difference. When it comes to working with hard plastic materials, there is a need for precision and efficiency. This is where the usage of specialized end mills for hard plastic comes into play. McMaster-Carr offers a wide range of end mills designed specifically for hard plastic machining. In this blog, we will explore the importance of using these end mills, discuss their different styles and sizes, and highlight the key benefits they bring to the table.Why Choose End Mills for Hard Plastic?Hard plastic materials such as acrylic, polycarbonate, and nylon pose unique challenges when it comes to machining. Regular end mills that are designed for working with metals may not provide optimal results in cutting, shaping, or drilling hard plastic. Using improper tools can lead to issues like melting, chipping, or even breaking of the material.This is where end mills specifically designed for hard plastic materials excel. These tools are built with specialized geometries and cutting edge designs that allow for efficient and precise machining of hard plastics. They enable clean cuts and smooth finishes without compromising the structural integrity of the plastic.Styles and Sizes for Every NeedMcMaster-Carr offers a wide selection of end mills for hard plastic, ensuring that you can find the perfect tool for your specific application. These end mills come in various styles and sizes, allowing you to cater to different machining requirements.Some common styles of end mills for hard plastic include single flute, double flute, and compression end mills. Single flute end mills work well for high-speed cutting and provide excellent chip evacuation. Double flute end mills are suitable for more intricate cutting and can handle both roughing and finishing operations. Compression end mills, on the other hand, are designed for reducing top surface burrs and work best on thin-walled materials.When it comes to sizes, McMaster-Carr offers an extensive range to suit different project needs. From small diameter end mills for detailed work to larger ones for heavy-duty operations, there is a size available for every application.Benefits of Using End Mills for Hard Plastic1. Improved Surface Finish: The specialized designs of end mills for hard plastic ensure a smoother surface finish, reducing the need for additional polishing or finishing processes.2. Reduced Material Waste: These end mills are built to efficiently cut through hard plastics, resulting in less material waste and increased productivity.3. Enhanced Tool Life: With their optimized designs, end mills for hard plastic are more resistant to wear and provide longer tool life, reducing the need for frequent tool changes.4. Precise Machining: Thanks to their geometries and cutting edge designs, these end mills allow for precise cuts, ensuring dimensional accuracy in your machined parts.5. Cost Savings: By using the right tools for the job, you can minimize material waste, improve efficiency, and reduce the need for secondary operations. This results in cost savings for your machining projects.ConclusionWhen it comes to machining hard plastics, having the right tools is essential. McMaster-Carr offers an extensive selection of end mills for hard plastic that cater to different styles, sizes, and applications. By choosing these specialized tools, you can achieve superior surface finishes, reduce material waste, enhance tool life, and ensure precise machining. So, unlock the full potential of hard plastic machining today with end mills specifically designed for the job. Trust in McMaster-Carr to provide the tools you need for successful and efficient hard plastic machining projects.
Top Quality Carbide Milling Cutters with Durability and Precision
Solid Carbide Milling Cutters: A Revolution in Precision Machining[Company Name], a renowned pioneer in the field of precision engineering, is proud to introduce its latest technological innovation – Solid Carbide Milling Cutters. With over [number of years] of experience in the industry, [Company Name] has always strived to provide cutting-edge solutions that enhance productivity and efficiency in machining processes. The introduction of Solid Carbide Milling Cutters is yet another testament to the company's commitment to innovation and continuous improvement.Traditional milling cutters have long been used in various industries for material removal and shaping processes. However, with the constant advancements in technology and the need for higher precision, conventional cutters often fall short. The limitations of these tools in terms of tool life, cutting speed, and overall performance have led to the development of more advanced alternatives. Solid Carbide Milling Cutters, with their exceptional properties and performance, have quickly become the preferred choice for precision machining applications.One of the key features that sets Solid Carbide Milling Cutters apart from their counterparts is their material composition. Made from a solid piece of high-quality carbide, these cutters exhibit outstanding durability and wear resistance. Carbide, known for its hardness and ability to withstand high temperatures, ensures that the cutting edges remain sharp and intact for extended periods of use. This exceptional tool life significantly reduces the need for frequent tool changes, decreasing downtime and increasing overall productivity.In addition to their durability, Solid Carbide Milling Cutters offer exceptional precision and surface finish. The high rigidity of carbide allows for stable and accurate machining, minimizing vibrations and ensuring dimensional accuracy. This unique characteristic makes these cutters ideal for applications that demand tight tolerances and superior surface quality. Industries such as aerospace, automotive, and medical, to name a few, can greatly benefit from the precision offered by Solid Carbide Milling Cutters.Moreover, Solid Carbide Milling Cutters are designed to accommodate various machining challenges, thanks to their versatility. With a wide range of tool geometries and flute designs available, these cutters can efficiently handle different material types, cutting depths, and feed rates. Whether it's milling soft aluminum alloys or high-tensile steel, Solid Carbide Milling Cutters offer optimal performance, ensuring increased productivity and reduced production costs.[Company Name]'s Solid Carbide Milling Cutters are not only known for their exceptional performance but also for their environmental sustainability. These cutters are designed to generate minimal waste and promote resource efficiency. The extended tool life reduces the frequency of tool replacements, resulting in less material waste. Additionally, the use of carbide, a recyclable material, aligns with [Company Name]'s commitment to minimizing the environmental impact of its products.To further ensure customer satisfaction, [Company Name] provides comprehensive technical support and customized solutions tailored to individual machining needs. With a team of highly skilled engineers and state-of-the-art facilities, the company guarantees the highest level of support throughout the entire machining process. From selecting the appropriate Solid Carbide Milling Cutter to optimizing cutting parameters, [Company Name] strives to deliver a seamless experience for its valued customers.In conclusion, [Company Name]'s introduction of Solid Carbide Milling Cutters marks a significant advancement in precision machining. These cutters, with their exceptional durability, precision, and versatility, are set to revolutionize the way industries approach material removal and shaping processes. With its focus on innovation and customer satisfaction, [Company Name] continues to establish itself as a leading provider of cutting-edge solutions in the field of precision engineering.