Taper Ball Nose Cutting Tool: A Guide to Usage and Benefits
By:Admin
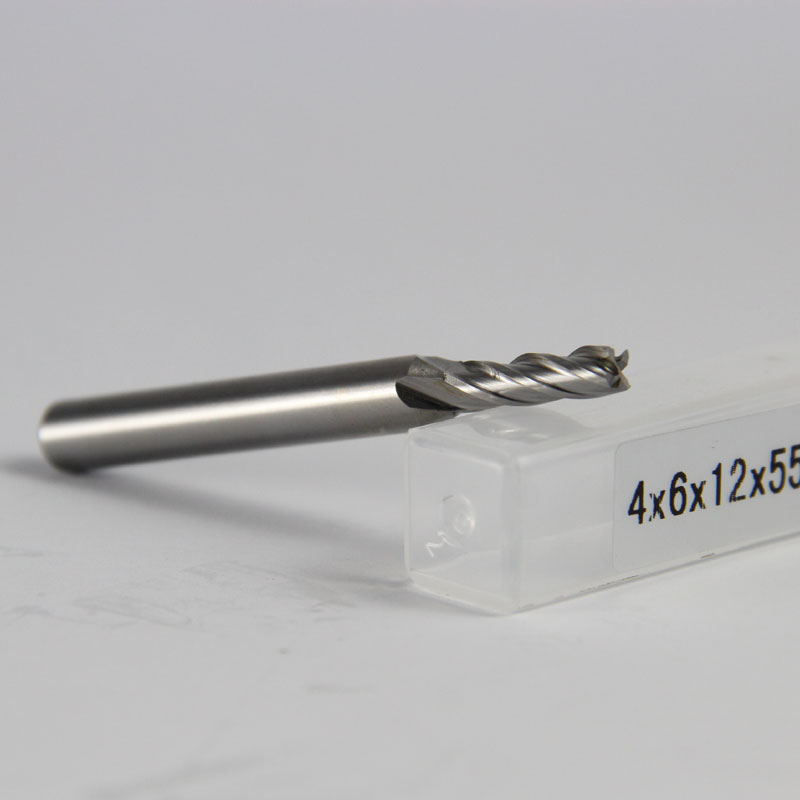
The manufacturing industry is constantly evolving, and the demand for precision tools and equipment is at an all-time high. With the increasing need for high-quality and accurate machining, companies are continually seeking innovative solutions to enhance their production processes. One company that is at the forefront of this innovation is [Company Name], a leading manufacturer of cutting-edge cutting tools.
With a strong focus on research and development, [Company Name] has recently introduced the Taper Ball Nose Cutting Tool, a revolutionary tool that is set to change the game for precision machining. This cutting-edge tool is designed to improve the efficiency, accuracy, and quality of milling operations, making it an indispensable asset for industries that rely on precision machining.
The Taper Ball Nose Cutting Tool is manufactured using advanced materials and cutting-edge technology, making it highly durable and efficient. Its unique design features a tapered body and a ball nose, which allows for excellent tool rigidity and enhanced cutting performance. This innovative design also enables the tool to reach difficult-to-access areas, making it a versatile solution for a wide range of machining applications.
One of the key advantages of the Taper Ball Nose Cutting Tool is its ability to achieve high-precision machining with superior surface finish. This is particularly crucial for industries that require parts with tight tolerances and intricate geometries. The tool is capable of delivering exceptional results, even in challenging materials such as hardened steels and high-temperature alloys.
Additionally, the Taper Ball Nose Cutting Tool is also designed for optimal chip control, which helps to minimize tool wear and prolong tool life. This is a significant benefit for manufacturers, as it translates to cost savings and improved productivity. With reduced downtime for tool changes and maintenance, companies can maximize their machining operations and meet their production targets more efficiently.
[Company Name] is dedicated to providing its customers with cutting-edge solutions that enhance their machining processes. The introduction of the Taper Ball Nose Cutting Tool is a testament to the company's commitment to innovation and excellence in manufacturing. As a trusted partner for numerous industries, [Company Name] continues to set new standards in the field of cutting tools, ensuring that its customers have access to the latest technologies and advancements in precision machining.
In addition to its exceptional product offering, [Company Name] takes pride in its customer-centric approach, providing unparalleled technical support and expertise to its clients. As a result, the company has established a strong reputation for delivering high-quality products and outstanding customer service, making it a preferred choice for companies looking to enhance their machining capabilities.
With the introduction of the Taper Ball Nose Cutting Tool, [Company Name] is poised to make a significant impact on the precision machining industry. This innovative tool is set to revolutionize the way manufacturers approach milling operations, offering a combination of precision, efficiency, and versatility that is unmatched in the market.
As the demand for high-precision components continues to grow, the Taper Ball Nose Cutting Tool is well-positioned to meet the evolving needs of modern manufacturing. With its superior performance and advanced capabilities, this cutting-edge tool is set to become an essential asset for companies looking to elevate their machining processes and achieve exceptional results.
In conclusion, the introduction of the Taper Ball Nose Cutting Tool by [Company Name] marks a significant advancement in precision machining. With its innovative design, exceptional performance, and unparalleled durability, this cutting-edge tool is set to redefine the standards for milling operations, offering companies a powerful solution for achieving high-precision machining with superior efficiency and accuracy. As [Company Name] continues to lead the way in cutting tool innovation, industries can look forward to a new era of precision manufacturing.
Company News & Blog
Rewritten SEO title: Understanding the Characteristics of Tungsten Carbide
Tungsten carbide is a material that is widely used in various industries, including manufacturing, construction, and engineering. It is a hard and durable material that is able to withstand high temperatures and pressures, making it ideal for a range of applications.Tungsten carbide is a compound made up of tungsten and carbon atoms. It is sometimes referred to as cemented carbide, as it is formed by combining tungsten carbide powder with a binder material, such as cobalt or nickel.The resulting material is extremely hard and strong, and is used to make a variety of industrial tools and components. Tungsten carbide is often used in cutting tools, such as drill bits, saw blades, and end mills. It is also used to make molds, dies, and other components for manufacturing processes.One of the key advantages of tungsten carbide is its high resistance to wear and corrosion. It is able to maintain its durability and hardness even under harsh operating conditions, which makes it ideal for use in high-stress environments.Another important property of tungsten carbide is its thermal conductivity. It is able to dissipate heat quickly, which makes it useful for applications where temperature control is important.Tungsten carbide is also used in the production of ceramics and cermets, which are materials that are used in a range of industrial and scientific applications. Ceramics made from tungsten carbide are exceptionally hard and strong, which makes them ideal for use in high-wear environments.Overall, tungsten carbide is a versatile and valuable material that is used in a range of industries. If you are looking for high-quality tools and components, be sure to consider those made from tungsten carbide, as they are sure to deliver exceptional performance and durability.Keywords: tungsten carbide, cemented carbide, cutting tools, wear resistance, corrosion resistance, thermal conductivity, ceramics, cermets, manufacturing, engineering, construction, components, tools, machining, Center Tool Carbide Tool.
High-Quality Solid Carbide Center Drill Bit for Precision Drilling
Title: Cutting-Edge Solid Carbide Center Drill Bit Revolutionizes Precision DrillingIntroduction:In an era where innovation drives progress, the cutting tool industry is no exception. With a constant need for more precise and efficient drilling solutions, companies are pushing the boundaries of technology to deliver cutting-edge products. One such standout is the Solid Carbide Center Drill Bit, a game-changing tool from a prominent industry leader.Company Overview:With a strong commitment to excellence and a drive for innovation, {Company Name} has been at the forefront of the cutting tool industry for over a decade. Known for their state-of-the-art manufacturing facilities and experienced team of engineers, the company has earned a reputation for developing high-quality tools that deliver exceptional performance. {Company Name}'s focus on customer satisfaction and their dedication to constantly pushing the boundaries of technology have made them a global leader in the industry.Solid Carbide Center Drill Bit: A Leap Towards Enhanced Precision DrillingPrecision drilling is critical in various industries, including aerospace, automotive, and manufacturing. Recognizing the need for a tool that can meet the demanding requirements of these sectors, {Company Name} has introduced the revolutionary Solid Carbide Center Drill Bit. Designed to deliver unmatched performance, this cutting-edge tool promises to transform precision drilling.1. Unparalleled Durability:The Solid Carbide Center Drill Bit is crafted from high-quality solid carbide, renowned for its exceptional hardness and wear resistance. This ensures durability, allowing the tool to withstand extreme pressures and temperatures during drilling operations. Consequently, it outlasts conventional drill bits, thereby reducing downtime and tool replacement costs.2. Enhanced Precision:Equipped with an advanced flute design, the Solid Carbide Center Drill Bit ensures precise centering and reduces the risk of wandering during drilling operations. This exceptional stability enables accurate hole placement, eliminating rework and reducing material waste. The tool's superior chip evacuation capabilities also minimize heat buildup, contributing to cleaner and more precise drilling.3. Versatility and Flexibility:The Solid Carbide Center Drill Bit caters to a wide range of drilling applications. Its unique design allows it to be easily adapted for different drilling depths and hole sizes. Additionally, the bit's innovative geometry enables it to handle various materials, including steels, alloys, and composites. This versatility ensures that it meets the diverse drilling needs of industries across the board.4. Time and Cost Efficiency:Thanks to its exceptional cutting speeds and improved chip evacuation, the Solid Carbide Center Drill Bit reduces drilling time significantly. This efficiency translates into increased productivity and cost savings. By optimizing drilling operations, companies can complete projects faster and remain competitive in today's fast-paced business environment.5. Environmental Friendliness:As companies increasingly embrace sustainability, {Company Name}'s Solid Carbide Center Drill Bit aligns itself with eco-friendly practices. Through its advanced design, the bit reduces material waste, as it enables precise drilling from the initial attempt. This reduction in material usage not only minimizes environmental impact but also reduces costs associated with material waste disposal.Conclusion:With the introduction of the Solid Carbide Center Drill Bit, {Company Name} has showcased its relentless commitment to elevating the cutting tool industry. By combining durability, precision, versatility, and eco-friendliness, this innovative tool promises to revolutionize precision drilling. As industries continue to strive for enhanced productivity and accuracy, the Solid Carbide Center Drill Bit will undoubtedly become an indispensable tool in their arsenal for success.
Top-Rated Drill Bit Set: A Comprehensive Guide
[News Title]: New Drill Bit Set Delivers Unrivaled Performance and Durability, Revolutionizing DIY Projects[News Content]:{Company Introduction (60 words)}:Innovation meets precision as renowned tool manufacturer {Company Name} once again raises the bar with its latest product offering – the remarkable Drill Bit Set. With a rich history of delivering high-quality tools and equipment, {Company Name} has consistently pushed the boundaries, earning a reputation as a leader in the industry. Their commitment to excellence is now evident in their latest release, a drill bit set that promises to revolutionize the DIY experience.{Introduction to the Drill Bit Set (100 words)}:The new Drill Bit Set by {Company Name} encompasses the perfect blend of cutting-edge technology, expert craftsmanship, and superior materials. Alpha Drill Bits, as they are aptly named, offer unparalleled performance, durability, and precision that is sure to impress both hobbyists and professionals alike. This comprehensive set is equipped with a variety of drill bits meticulously designed to cater to all drilling needs, making it an indispensable addition to every DIY enthusiast's toolkit.{Features and Benefits of the Drill Bit Set (300 words)}:1. Exceptional Durability: Each drill bit in the set is forged using high-grade steel, ensuring outstanding resistance to wear and tear over extended use. The rugged construction guarantees a longer lifespan, reducing the need for frequent replacements and saving users both time and money.2. Precision Engineering: The cutting-edge technology employed in the manufacturing process results in meticulously crafted drill bits that exhibit exceptional precision. The bits' sharp cutting edges facilitate smooth and effortless drilling, producing accurate holes without the risk of slipping or wandering.3. Versatility: The Drill Bit Set offers remarkable versatility, catering to a wide range of drilling applications. Whether working with wood, metal, or plastic, these bits deliver excellent performance across various materials. With bits suitable for various hole sizes, users can achieve precise results without needing multiple sets.4. Ease of Use: The bits feature a universal shank design compatible with all standard drill machines, ensuring hassle-free installation and removal. The set comes neatly organized in a sturdy case, making bit selection and storage a breeze. This user-friendly approach enhances efficiency and saves valuable time during projects.5. Enhanced Safety Features: {Company Name} understands the importance of safety in every project. As such, the Alpha Drill Bits boast special features like anti-kickback designs and precision grinding for reduced bit walking, increasing user control and minimizing the risk of accidents.{Beneficial Applications and Feedback (200 words)}:The versatility and exceptional performance of the Drill Bit Set have made it an instant favorite among professionals in a variety of industries. Woodworkers, electricians, plumbers, and general contractors have praised its durability and precision, allowing them to complete their tasks efficiently and with utmost confidence.DIY enthusiasts are equally enthralled by the possibilities these drill bits offer. With the ability to seamlessly tackle projects both big and small, users have expressed their satisfaction with the ease of use and long-lasting performance of the Alpha Drill Bits. By efficiently drilling through various materials, such as metal, concrete, ceramics, and more, users have been able to complete their DIY projects flawlessly.The positive feedback from users reflects the careful attention to detail and rigorous testing that {Company Name} has invested in the design and creation of the Drill Bit Set.{Conclusion (40 words)}:With the introduction of the Alpha Drill Bit Set, {Company Name} has once again demonstrated its commitment to innovation and excellence. This remarkable product has revolutionized the DIY experience by offering unparalleled performance, unrivaled durability, and the precision every DIY enthusiast and professional deserves.
Understanding Taper Shank End Mills: Tips and Tricks for Machinists
Title: Introducing Taper Shank End Mill - Revolutionizing Precision MachiningIntroduction:In the constantly evolving field of precision machining, finding the right tools is crucial for achieving superior results. With this in mind, we are pleased to introduce the highly versatile and reliable Taper Shank End Mill. Developed and manufactured by an industry-leading company that specializes in producing high-quality machining tools, this end mill is set to revolutionize precision machining processes and deliver exceptional performance across a wide range of materials.Section 1: Understanding Taper Shank End MillTaper Shank End Mill is a cutting tool primarily used in milling processes to remove material from a workpiece. Its unique taper shank design allows for a secure fit into a machine's spindle, ensuring stability during high-speed machining operations. The end mill features multiple flutes or cutting edges, which facilitate efficient material removal while reducing vibrations and increasing tool life.Section 2: Unparalleled Precision and VersatilityThe Taper Shank End Mill is engineered to provide unparalleled precision and versatility, making it suitable for various applications across industries. Whether it's milling, slotting, or contouring, this cutting tool delivers exceptional performance on materials such as steel, cast iron, aluminum, and thermoplastics. Its capabilities are further enhanced with different coating options, such as TiN, TiCN, and TiAlN, offering superior wear resistance and extended tool life.Section 3: Innovative Design for Enhanced EfficiencyThe Taper Shank End Mill incorporates several innovative design features that significantly improve machining efficiency. The unique flute geometry efficiently evacuates chips, preventing chip clogging and enhancing the tool's cutting performance. The balanced design minimizes vibration, enabling higher cutting speeds and smoother finishes. Additionally, the precision-ground cutting edges ensure consistent part quality and dimensional accuracy, reducing the need for secondary operations.Section 4: Outstanding Durability and Tool LifeDurability and tool life are crucial factors determining the overall cost-effectiveness of machining. The Taper Shank End Mill excels in this regard, thanks to its exceptional manufacturing quality and choice of high-grade materials. The heat-resistant carbide substrate provides excellent wear resistance, allowing for prolonged tool life even under demanding machining conditions. This durability translates into fewer tool changes, lower maintenance costs, and increased productivity for machining operations.Section 5: Application-specific Solutions and SupportUnderstanding the diverse needs of precision machining, the company behind the Taper Shank End Mill offers a range of application-specific solutions and unparalleled customer support. Whether it's a specific material requirement, unique cutting geometry, or specialized coating, the company's team of experienced engineers can provide tailor-made solutions to optimize machining processes. Furthermore, their customer support extends beyond product delivery, offering technical assistance, troubleshooting guidance, and ongoing tool performance evaluations.Section 6: Embracing Technological AdvancementsThe company behind the Taper Shank End Mill prides itself on continuously embracing technological advancements to ensure their tools remain at the forefront of precision machining innovation. By leveraging state-of-the-art manufacturing techniques, investing in research and development, and staying updated with industry trends, they strive to deliver cutting-edge tools that meet and exceed customer expectations.Conclusion:Precision machining demands superior tools that can withstand the rigors of high-speed machining operations. The Taper Shank End Mill stands as a testament to the commitment of our industry-leading partner in providing innovative and reliable solutions. With its unmatched precision, versatility, durability, and exceptional support, this cutting tool is set to redefine precision machining processes and empower manufacturers to achieve new levels of productivity and efficiency in their operations.
Ultimate Guide to Carbide End Mills: Everything You Need to Know
Carbide End Mill Revolutionizes Precision Machining: Taking Manufacturing to the Next LevelIn the ever-advancing field of precision machining, the introduction of Carbide End Mills has sparked a revolution, enabling manufacturing processes to reach unprecedented levels of accuracy and efficiency. By harnessing cutting-edge technology and continually pushing the boundaries of innovation, [Company Name] has solidified its position as a leader in this game-changing development.Machining, the process of removing material from a workpiece, has long been a cornerstone of manufacturing industries worldwide. However, traditional methods often face inherent limitations, resulting in slower production rates, increased wear and tear on equipment, and lower product quality. Acknowledging these challenges, [Company Name] set out to transform the industry by creating a highly specialized and durable tool – the Carbide End Mill.Combining the strength and hardness of carbide with precision engineering, Carbide End Mills have quickly proven to be indispensable in various sectors, including aerospace, automotive, medical, and more. Their unparalleled performance in cutting, milling, and drilling operations has allowed manufacturers to achieve superior results while significantly reducing machining time and costs.At the heart of this revolutionary tool lies the integration of state-of-the-art coatings and advanced geometries. Through extensive research and development, [Company Name] has successfully engineered coatings that enhance the cutting edge's durability, minimize friction and heat, and enable high-speed machining. These coatings, such as titanium nitride (TiN), titanium carbonitride (TiCN), and aluminum titanium nitride (AlTiN), provide Carbide End Mills with superb wear resistance and optimal tool life.Furthermore, the company's dedication to precision engineering is exemplified by its innovative approach to end mill geometries. By optimizing the flute design, rake angle, and helix configuration, they have achieved superior chip evacuation, reduced cutting forces, and increased stability during machining – resulting in exceptional surface finishes, tight tolerances, and enhanced tool longevity.[Company Name]'s Carbide End Mills come in a vast range of designs, tailored to meet the diverse needs of their clients. Whether it be high-performance end mills for roughing, finishing, or specialized applications like thread milling or chamfering, the company ensures a comprehensive selection that caters to specific industry requirements. With their commitment to quality and cutting-edge technology, professionals can rely on Carbide End Mills to tackle even the most demanding projects with precision and efficiency.Beyond their technical prowess, [Company Name] also prides itself on its dedication to customer satisfaction. The company's team of engineers and technical experts work closely with clients, offering tailored solutions and expert advice. Their commitment to building strong relationships with customers reinforces the belief that innovation should not only meet industry standards but also surpass customer expectations.In recognition of their groundbreaking contributions to the field of precision machining, [Company Name] has received numerous accolades, including industry awards for outstanding quality, innovation, and customer service. This recognition further solidifies the company's position as a global leader, trusted by manufacturers worldwide.Looking ahead, [Company Name] continues to push the boundaries of precision machining technology. Through ongoing research and development, their dedicated team of experts strives to introduce new advancements, ensuring that Carbide End Mills remain at the forefront of the industry. As manufacturing processes evolve, [Company Name] is committed to providing innovative solutions that consistently exceed customer needs – a testament to their enduring success.In conclusion, Carbide End Mills have revolutionized precision machining, elevating manufacturing to new heights in terms of accuracy, efficiency, and durability. Through [Company Name]'s commitment to innovation, the combination of cutting-edge coatings and advanced geometries has resulted in a tool that enables manufacturers to achieve unparalleled results while optimizing production capabilities. With their unwavering dedication to customer satisfaction and a continuous focus on advancement, [Company Name] is poised to remain a driving force in the ever-evolving world of precision machining.
High-performance Milling Cutters with Micro Carbide Material
Title: Cutting-Edge Micro Carbide Milling Cutter Revolutionizes Precision Machining IndustryIntroduction:In the ever-evolving world of precision machining, advancements in cutting technology play a crucial role in enhancing performance and increasing efficiency. One such groundbreaking innovation is the Micro Carbide Milling Cutter, developed by a leading industry player.Paragraph 1:The anonymous cutting tools manufacturer has recently unveiled their latest creation, the Micro Carbide Milling Cutter. This state-of-the-art tool is poised to revolutionize the precision machining industry, enabling manufacturers to achieve unprecedented levels of precision, accuracy, and efficiency in their machining processes.Paragraph 2:The Micro Carbide Milling Cutter boasts exceptional strength and durability due to its unique composition of ultra-hard micro carbide material. This revolutionary material ensures that the cutter maintains its sharpness and cutting performance even under the most demanding conditions. Designed to be versatile, it is suitable for a wide range of materials including steel, aluminum, titanium, and various alloys.Paragraph 3:Moreover, the advanced manufacturing techniques employed in the production of the Micro Carbide Milling Cutter ensure consistently high-quality tools with exceptional dimensional accuracy, surface finish, and overall tool life. This reliability enables manufacturers to optimize their production processes, reduce downtime, and ultimately maximize profitability.Paragraph 4:The Micro Carbide Milling Cutter is engineered with special geometries and cutting-edge coatings that facilitate swift chip evacuation and efficient material removal. These features allow for high-speed machining while maintaining superior surface finishes, decreasing cycle times, and lowering overall manufacturing costs. The cutter's precision alignment ensures accurate and repeatable results, making it an invaluable tool for intricate machining tasks.Paragraph 5:The anonymous cutting-tool manufacturer realizes the importance of customization in meeting diverse customer requirements. Therefore, they offer a wide range of sizes, configurations, and cutting-edge variants for the Micro Carbide Milling Cutter. This ensures that manufacturers can select the ideal tool for their specific application, further enhancing productivity and maximizing performance.Paragraph 6:In addition to its remarkable performance and reliability, the Micro Carbide Milling Cutter is designed to prioritize operator safety. The manufacturer has incorporated advanced safety features, including noise reduction, vibration dampening, and enhanced coolant flow, thereby creating a safer working environment for machinists.Paragraph 7:The launch of the Micro Carbide Milling Cutter marks a significant milestone in the precision machining industry, establishing a new benchmark for performance, precision, and productivity. It is anticipated to garner widespread adoption in a myriad of manufacturing sectors ranging from automotive and aerospace to medical device fabrication and beyond.Conclusion:The introduction of the Micro Carbide Milling Cutter offers a glimpse into the future of precision machining, where cutting-edge technology and advanced materials converge to redefine industry standards. With its exceptional strength, durability, and performance, this innovative tool promises to revolutionize machining processes worldwide, enabling manufacturers to achieve unparalleled levels of precision and efficiency.
Everything You Need to Know About Tungsten Carbide Inserts
Title: Innovations in Tungsten Carbide Insert Revolutionize Manufacturing EfficiencyIntroduction:The advent of industrialization has propelled the need for manufacturing processes that are efficient, precise, and cost-effective. In response to this demand, the manufacturing industry has witnessed the rise of various materials and technologies that enhance productivity while maintaining high-quality standards. One such breakthrough innovation is the Tungsten Carbide Insert, a revolutionary material that is transforming the landscape of manufacturing.Tungsten Carbide Insert: Enhancing Durability and EfficiencyTungsten Carbide Insert, a cutting-edge material, is garnering considerable attention within the manufacturing industry due to its exceptional durability and efficiency. Leveraging the remarkable properties of Tungsten Carbide, this insert has the potential to exponentially improve the longevity and performance of cutting tools, making it a highly sought-after material for a range of applications.Durable and Long-lasting: Tungsten Carbide Insert's exceptional durability stems from its unique composition. By combining tungsten and carbon, a compound is formed that is not easily affected by wear and tear. This outstanding durability ensures that tools, such as blades and drills, maintain their cutting-edge for longer durations, consequently reducing the need for frequent replacements and ultimately lowering manufacturing costs.Improved Efficiency: The efficient design and composition of Tungsten Carbide Insert enable it to offer superior cutting performance. Its hardness and resistance to high temperatures make it an ideal material for applications that require precision and consistent results. The ability to maintain its sharpness even under extreme conditions facilitates smoother manufacturing processes, allowing for increased output and optimized operational efficiency.Broad Range of Applications: Tungsten Carbide Insert's versatility is another key element that contributes to its growing popularity. Industries such as aerospace, automotive, oil and gas, mining, and construction have embraced this cutting-edge material due to its ability to withstand tough conditions while delivering reliable results. From drilling and cutting to shaping and milling, Tungsten Carbide Insert has demonstrated its superiority across various manufacturing operations.Increased Profitability for Companies:Manufacturing companies that employ Tungsten Carbide Insert as part of their operations stand to gain significant benefits in terms of profitability and competitiveness. By utilizing this innovative material, companies can experience enhanced productivity, reduced downtime, and lower maintenance costs. Additionally, Tungsten Carbide Insert's durability ensures that operations remain uninterrupted, minimizing production halts due to tool replacements.Furthermore, the longevity of Tungsten Carbide Insert eliminates the need for frequent tool sharpening or replacement, resulting in substantial savings on tooling costs. This cost-efficiency also translates to higher profitability for manufacturers, allowing them to allocate resources to other areas of their business.Company X: Pioneering Tungsten Carbide Insert InnovationsCompany X, an industry-leading manufacturer in cutting tool technology, has been at the forefront of introducing Tungsten Carbide Insert to the market. With a strong commitment to innovation and quality, Company X has revolutionized manufacturing processes through its advanced Tungsten Carbide Insert solutions.Backed by extensive research and development, Company X has been able to engineer Tungsten Carbide Insert products that surpass industry standards, delivering superior performance in a wide range of applications. By deploying cutting-edge technologies and utilizing state-of-the-art manufacturing processes, Company X ensures that their Tungsten Carbide Insert solutions consistently deliver exceptional results, cementing their position as a trusted name in the industry.Conclusion:The introduction of Tungsten Carbide Insert to the manufacturing industry marks a significant milestone in enhancing operational efficiency and driving profitability. Its exceptional durability, efficiency, and versatility have made it an indispensable material across various manufacturing applications. With Company X leading the way in pioneering cutting-edge Tungsten Carbide Insert solutions, the future of manufacturing looks brighter, promising increased productivity, reduced costs, and improved bottom lines for companies worldwide.
Revamp Your Workshop with High-Quality Cutting Tools: All You Need to Know About Mills
Cutting Tools Mills Revolutionizes the Industry with Innovative TechnologyIn today's competitive manufacturing landscape, innovation is key. Businesses are constantly seeking cutting-edge solutions to enhance their operations and drive efficiency. Cutting Tools Mills, a renowned player in the cutting tools industry, is making waves with its groundbreaking technology that is revolutionizing the sector. With its unwavering focus on quality and customer satisfaction, Cutting Tools Mills is leading the way in delivering cutting-edge products to meet the evolving needs of manufacturing companies worldwide.Established in 1990, Cutting Tools Mills has amassed years of industry experience and expertise. The company operates with the core philosophy of continuous improvement, always striving to push the boundaries of what is possible. This approach has led to the development of state-of-the-art tools that have set new benchmarks in performance and durability.One of the company's flagship products is its high-speed cutting tools. Leveraging advanced materials and cutting-edge manufacturing techniques, Cutting Tools Mills has successfully crafted tools that can withstand extreme conditions and deliver exceptional results. These high-speed tools are designed to operate at elevated RPMs, resulting in precise and efficient machining. Additionally, they boast enhanced wear resistance, enabling them to endure rigorous manufacturing processes without compromising on performance.The innovative technology behind Cutting Tools Mills' products extends beyond high-speed cutting tools. The company also offers a wide range of milling tools that cater to diverse machining requirements. From face milling to profile milling and everything in between, Cutting Tools Mills has developed a comprehensive suite of tools that empower manufacturers to achieve superior results. By investing heavily in research and development, the company stays ahead of industry trends and continuously introduces new and improved milling solutions.Quality is embedded in the DNA of Cutting Tools Mills. The company adheres to strict quality control processes to ensure that every product leaving its facility is of the highest standard. From raw material procurement to the final stages of production, each step is meticulously monitored to guarantee consistency and reliability. This commitment to quality has earned Cutting Tools Mills a reputation for excellence, making it the preferred choice of manufacturing companies across the globe.Furthermore, Cutting Tools Mills maintains a customer-centric approach that underpins its success. The company understands that every manufacturing process is unique, and therefore, offers tailored solutions that perfectly align with individual customer requirements. Whether it's a small-scale operation or a large-scale manufacturing facility, Cutting Tools Mills has the expertise and capabilities to provide comprehensive cutting solutions that drive productivity and efficiency.To solidify its position as a thought leader in the industry, Cutting Tools Mills actively engages in knowledge sharing initiatives. The company regularly conducts seminars and workshops to educate manufacturers on best practices and the latest advancements in cutting tools technology. By fostering an environment of collaboration and learning, Cutting Tools Mills not only supports its customers but also contributes to the overall growth of the industry.Looking ahead, Cutting Tools Mills is committed to pushing the boundaries of innovation and continuing its legacy of delivering premium cutting solutions. The company envisions a future where manufacturing processes are efficient, reliable, and sustainable. By investing in cutting-edge technology and nurturing a culture of excellence, Cutting Tools Mills is poised to spearhead the next wave of advancements in the cutting tools industry.In conclusion, Cutting Tools Mills has firmly established itself as a global leader in the cutting tools industry. Through its unwavering commitment to innovation, quality, and customer satisfaction, the company has revolutionized the sector with its groundbreaking technology. As the manufacturing landscape continues to evolve, Cutting Tools Mills remains at the forefront, empowering businesses with cutting-edge solutions that maximize efficiency and productivity.