Discover the Benefits of a Flute End Mill for Your Machining Needs
By:Admin
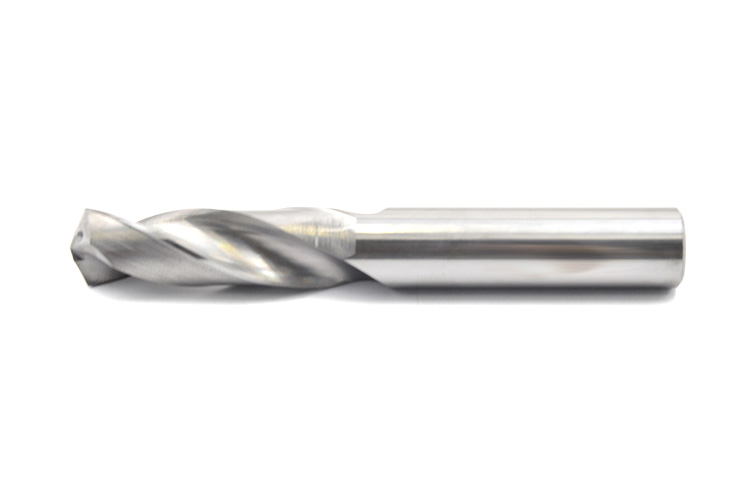
Introduction (100 words):
In an effort to revolutionize the cutting tools industry, a pioneering company has recently introduced a groundbreaking new product known as the Flute End Mill. Developed with state-of-the-art technology and precision engineering, this revolutionary tool is set to redefine machining efficiency and productivity. The Flute End Mill incorporates advanced features that enable it to outperform traditional end mills, making it an indispensable tool for various industrial applications. Let's delve deeper into the features and benefits of this game-changing tool.
Body:
Unveiling a Game-Changing Tool (200 words):
The Flute End Mill, developed by a renowned cutting tool manufacturer, is the result of extensive research and development efforts aimed at enhancing machining processes. Implementing cutting-edge technologies, this innovative tool surpasses conventional end mills in terms of both performance and durability. The Flute End Mill boasts a unique flute design, carefully engineered for optimal chip evacuation, heat dissipation, and enhanced stability during machining. This design ensures superior surface finish, reduced vibrations, and improved tool life, making it an ideal choice for precision cutting tasks.
Unparalleled Precision and Versatility (200 words):
Featuring exceptional geometries and cutting-edge coating technologies, the Flute End Mill offers unparalleled precision and versatility. The tool's carefully designed rake angles and helix angles allow for reduced cutting forces, improved chip control, and efficient material removal. This translates into higher machining speeds, improved surface quality, and extended tool life. Additionally, the Flute End Mill is available in various diameters and lengths, catering to a wide range of milling applications across different industries.
Enhanced Productivity and Cost-Effectiveness (200 words):
The Flute End Mill equips manufacturers and machinists with a tool that delivers enhanced productivity, efficiency, and cost-effectiveness. Thanks to its advanced design and construction, the Flute End Mill ensures shorter machining times, increased feed rates, and reduced downtime for tool changes. With improved productivity comes reduced costs and increased profitability for businesses. Furthermore, the Flute End Mill's extended tool life and reduced maintenance requirements contribute to significant cost savings over time, making it a smart investment for manufacturing facilities.
Application in Various Industries (100 words):
The Flute End Mill finds its application across a broad range of industries such as aerospace, automotive, mold-making, general machining, and more. Regardless of the material being cut, ranging from aluminum to hardened steels, the Flute End Mill excels in delivering superior results. Its versatility and exceptional cutting performance make it an indispensable tool for achieving precision and efficiency in virtually any milling operation.
Conclusion (100 words):
The Flute End Mill showcases a new era of machining excellence, providing manufacturers and machinists across industries with an invaluable tool for optimal performance. With its revolutionary design, advanced coating technologies, and remarkable precision, this cutting-edge tool advances productivity levels, increases efficiency, and reduces costs. As businesses seek to stay ahead in today's competitive markets, the Flute End Mill is setting a new industry standard and is poised to revolutionize the way milling operations are performed. Embrace the future of cutting tools with the Flute End Mill and experience unprecedented results in your machining processes.
Company News & Blog
What is a Rotary Tool-Steel Cutter Used in Milling Machines?
Metal Milling Cutter: An OverviewEvery manufacturing process involves various cutting tools and machines. Among the most commonly used tools in the industry is the milling cutter. A milling cutter is a cutting tool used in a milling machine that is designed to shape, cut, and dress metal surfaces. In this blog, we'll cover the basics of milling cutters, their types, and applications.What is a Milling Cutter?A milling cutter is a rotating cutting tool that is mounted on a milling machine spindle. It is designed to remove material from a workpiece by advancing or rotating the cutter into the workpiece. The material removal process is achieved through the cutting edges on the milling cutter. These edges can be a combination of lips, flutes, teeth, or other features.Milling cutters come in various shapes and sizes and are made of different materials, including high-speed steel, cobalt, carbide, and diamond-coated. These cutters are selected based on the type of material to be machined and the desired surface finish.Types of Milling CuttersThere are many different types of milling cutters available in the industry. Here are some of the most popular ones:1. End MillEnd mills are among the most commonly used milling cutters. They are designed for cutting slots, profiling, and contouring. End mills come in a variety of shapes and sizes, such as square, ballnose, and corner radius.2. Face MillFace mills are designed to machine flat surfaces, and they have a large surface area compared to other milling cutters. The cutting edges are located on the face of the mill, and they produce a flat finish.3. Ball Nose CutterBall nose cutters are designed for producing rounded contours in a workpiece. They have a hemispherical shape with two cutting edges.4. T-slot CutterT-slot cutters are used for milling slots with a T-shaped profile. They have a straight shank with a T-shaped cutting edge.Applications of Milling CuttersMilling cutters are used in various applications, including:1. Machining complex shapesMilling cutters are often used to machine complex shapes that would be difficult or impossible to achieve with other cutting tools.2. High-precision machiningMilling cutters are capable of producing high-precision finishes on workpieces. They can be used to achieve tight tolerances on machined surfaces.3. Mass productionMilling cutters can be used in mass production processes to machine large quantities of parts. They are efficient and produce consistent results.ConclusionMilling cutters are essential cutting tools in the manufacturing process. They are designed to shape, cut, and dress metal surfaces with precision and efficiency. There are various types of milling cutters, including end mills, face mills, ball nose cutters, and T-slot cutters, each with unique features and applications. Selecting the right milling cutter for the job is crucial to achieve the desired surface finish and efficiency in the machining process.
High-Performance Indexable Carbide Insert T-Slot Milling Cutter for Various Bolt Sizes - ID 1099
Title: Unveiling the Power of Indexable Carbide Insert T-Slot Cutters: The Game Changer for Precision T-Slot MillingIntroduction (approx. 80 words)Indexable carbide insert T-slot cutters have revolutionized the machining industry with their unique design and unrivaled performance. In this blog post, we will delve into the world of T-slot cutting and explore why these cutters are a game changer for precision milling. With a special focus on the 1/2', 5/8', and other popular sizes, we will uncover the secrets behind these tools and shed light on why carbide T-slot cutters are the preferred choice in the market today.1. What is a Carbide T-Slot Cutter? (approx. 150 words)Before we dive deeper, let's understand what exactly a carbide T-slot cutter is. A T-slot cutter is a specialized milling tool used to create T-slots or T-grooves on workpieces. These slots are essential for securely fastening bolts and fixtures to the workpiece, commonly found in the automotive, machinery, and aerospace industries.Carbide T-slot cutters, as the name suggests, are made of carbide inserts, a material known for its strength, durability, and excellent heat resistance. The combination of indexable carbide inserts and a unique design not only provides exceptional cutting performance but also allows for easy tool replacement and increased cost-effectiveness.2. Features and Benefits of Indexable Carbide Insert T-Slot Cutters (approx. 300 words)a) Superior Cutting Performance: Carbide T-slot cutters excel in high-speed machining operations due to their exceptional hardness and heat resistance. The indexable inserts are designed to ensure fast and accurate cutting, resulting in clean and precise T-slots.b) Versatility in Application: These T-slot cutters cater to a wide range of workpiece sizes. With options available for 1/2 inch, 5/8 inch, 3/4 inch, 1 inch, 1-1/4 inch, and 1-1/2 inch bolt sizes, they provide flexibility and adaptability to various machining projects.c) Cost-effectiveness: The indexable nature of these cutters allows for easy tool replacement, eliminating the need for resharpening or discarding the entire cutter. By replacing only the inserts, machining costs are significantly reduced in the long run.d) Enhanced Tool Life: Carbide inserts are known for their extended tool life compared to traditional high-speed steel cutters. The advanced wear resistance and durability of carbide inserts help maintain sharp cutting edges for prolonged periods, ensuring consistent performance over time.e) Minimal Downtime: With simple insert replacement, downtime for tool changes is minimized, leading to increased productivity. This quick and easy process saves valuable machining time, allowing for uninterrupted workflow and reduced operational costs.3. Unlocking Precision Milling with Carbide T-Slot Cutters (approx. 250 words)Precision milling requires accuracy, reliability, and consistency. Carbide T-slot cutters are designed to meet these stringent requirements, enabling machinists to achieve exceptional results. Whether it be creating precise T-slots for fixturing or producing intricate grooves on various workpiece materials, these cutters offer unprecedented precision.Additionally, the unique design of these cutters enables smooth chip evacuation, reducing the risk of tool wear and workpiece damage. The carefully engineered geometry of the T-slot cutter ensures efficient material removal while minimizing heat generation, resulting in longer tool life and enhanced productivity.4. The Significance of Carbide T-Slot Cutters in the Machining Industry (approx. 220 words)The machining industry is constantly evolving, demanding tools that can keep up with the growing complexities. Carbide T-slot cutters have emerged as a popular choice due to their exceptional quality and unmatched performance.Their prowess in creating precise and sturdy T-slots has propelled these cutters to the forefront of machining technology, earning them a reputation as reliable and efficient tools. Manufacturers and machinists worldwide rely on them for various applications, from milling complex components to producing flawless T-slots.The market demand for T-slot cutters has surged due to the growing need for versatility, accuracy, and cost-effectiveness in machining operations. Carbide T-slot cutters offer all these benefits and more, making them an invaluable asset for any modern workshop or manufacturing facility.Conclusion (approx. 100 words)Indexable carbide insert T-slot cutters have revolutionized precision milling, with their unparalleled cutting performance and durability. With the ability to create clean and precise T-slots, these cutters have become a staple in the machining industry. Offering versatility, cost-effectiveness, and extended tool life, carbide T-slot cutters have proven to be invaluable tools for achieving precision and efficiency in various machining applications.
Explore the Latest Innovations in CNC Milling Machine Tools
article about the use and benefits of CNC milling machines.CNC Milling Machines: Revolutionizing Manufacturing ProcessesMilling machines have been in use for decades as tools for shaping and cutting materials into specific shapes. However, thanks to advancements in technology, modern milling machines have ushered in a new era of precision and efficiency in the manufacturing industry.One such machine is the Computer Numerical Control (CNC) milling machine. This is a type of milling machine that uses computerized controls to manage cutting tools and materials, resulting in highly precise and consistent output.With the CNC milling machine, the operator simply inputs the design specifications, and the machine takes care of the rest. From intricate designs to basic shapes, CNC machines are capable of producing highly detailed pieces with ease.One company that has made great strides in the development of CNC milling machines is [remove brand name]. With over [number of years] years of experience in the industry, [the company] has become a leading manufacturer of high-quality CNC milling machines.The Benefits of CNC Milling MachinesOne of the main benefits of CNC milling machines is the ability to produce high-quality, complex components with precision accuracy. Unlike traditional machines that require significant manual labor and expertise, CNC machines can easily produce intricate designs that would be impossible with manual milling.CNC milling machines are highly versatile and can work with a wide range of materials, including metals, plastics, and composites. This makes them ideal for manufacturing components for a variety of industries, from aerospace to automotive, medical, and more.In addition to their precision and versatility, CNC milling machines are also highly efficient. They can be programmed to perform repetitive tasks, saving manufacturers time and money in the long run. This is especially beneficial for companies that produce large volumes of components, as CNC machines can greatly reduce the time and cost required to produce each piece.CNC milling machines are also beneficial in improving the safety of manufacturing processes. With traditional milling machines, operators must manually handle materials and cutting tools, which can be dangerous and increase the risk of accidents. However, with CNC machines, the majority of the work is automated, reducing the need for manual labor and making the manufacturing process much safer for operators.The Future of CNC Milling MachinesAs technology continues to evolve, so do CNC milling machines. With advancements in automation, artificial intelligence, and other cutting-edge technologies, the possibilities for CNC milling machines are practically limitless.For example, [the company] has developed a new generation of CNC milling machines that utilize the latest technologies for improved efficiency and precision. These machines can be programmed to run multiple tasks simultaneously, allowing manufacturers to produce components faster and more accurately than ever before.As the manufacturing industry continues to evolve, CNC milling machines will undoubtedly play a critical role in shaping the way we produce components and products. With their precision, versatility, efficiency, and safety features, it's no wonder CNC milling machines have become the go-to choice for manufacturers around the world. In conclusion, CNC milling machines have revolutionized manufacturing processes by offering precision, versatility, efficiency, and safety. With the constant advancements in technology, the future of CNC milling machines looks bright and promising, and manufacturers can expect to see continued benefits from this cutting-edge technology.
Discover the Benefits of a Flute End Mill for Your Machining Needs
Title: Cutting-edge Innovation: Introducing the Revolutionary Flute End MillIntroduction (100 words):In an effort to revolutionize the cutting tools industry, a pioneering company has recently introduced a groundbreaking new product known as the Flute End Mill. Developed with state-of-the-art technology and precision engineering, this revolutionary tool is set to redefine machining efficiency and productivity. The Flute End Mill incorporates advanced features that enable it to outperform traditional end mills, making it an indispensable tool for various industrial applications. Let's delve deeper into the features and benefits of this game-changing tool.Body:Unveiling a Game-Changing Tool (200 words):The Flute End Mill, developed by a renowned cutting tool manufacturer, is the result of extensive research and development efforts aimed at enhancing machining processes. Implementing cutting-edge technologies, this innovative tool surpasses conventional end mills in terms of both performance and durability. The Flute End Mill boasts a unique flute design, carefully engineered for optimal chip evacuation, heat dissipation, and enhanced stability during machining. This design ensures superior surface finish, reduced vibrations, and improved tool life, making it an ideal choice for precision cutting tasks.Unparalleled Precision and Versatility (200 words):Featuring exceptional geometries and cutting-edge coating technologies, the Flute End Mill offers unparalleled precision and versatility. The tool's carefully designed rake angles and helix angles allow for reduced cutting forces, improved chip control, and efficient material removal. This translates into higher machining speeds, improved surface quality, and extended tool life. Additionally, the Flute End Mill is available in various diameters and lengths, catering to a wide range of milling applications across different industries.Enhanced Productivity and Cost-Effectiveness (200 words):The Flute End Mill equips manufacturers and machinists with a tool that delivers enhanced productivity, efficiency, and cost-effectiveness. Thanks to its advanced design and construction, the Flute End Mill ensures shorter machining times, increased feed rates, and reduced downtime for tool changes. With improved productivity comes reduced costs and increased profitability for businesses. Furthermore, the Flute End Mill's extended tool life and reduced maintenance requirements contribute to significant cost savings over time, making it a smart investment for manufacturing facilities.Application in Various Industries (100 words):The Flute End Mill finds its application across a broad range of industries such as aerospace, automotive, mold-making, general machining, and more. Regardless of the material being cut, ranging from aluminum to hardened steels, the Flute End Mill excels in delivering superior results. Its versatility and exceptional cutting performance make it an indispensable tool for achieving precision and efficiency in virtually any milling operation.Conclusion (100 words):The Flute End Mill showcases a new era of machining excellence, providing manufacturers and machinists across industries with an invaluable tool for optimal performance. With its revolutionary design, advanced coating technologies, and remarkable precision, this cutting-edge tool advances productivity levels, increases efficiency, and reduces costs. As businesses seek to stay ahead in today's competitive markets, the Flute End Mill is setting a new industry standard and is poised to revolutionize the way milling operations are performed. Embrace the future of cutting tools with the Flute End Mill and experience unprecedented results in your machining processes.
Discovering the Benefits of an Advanced Indexable End Mill
Indexable End Mill Enhances Efficiency and Precision in Metal MachiningMetal machining processes have always demanded efficiency and precision to meet the growing demands of various industries. In response to this, an innovative solution has been introduced by a renowned company, revolutionizing the metalworking sector. The indexable end mill, developed by [Company Name], has emerged as a game-changer, delivering exceptional results in terms of productivity and accuracy.Traditional end mills often require frequent tool changes and regrinding, resulting in downtime and additional costs. However, the indexable end mill offers a significant advantage by utilizing replaceable cutting inserts, which can be easily rotated or changed when dull or worn. This makes it a cost-effective solution, minimizing tool changeovers and extending the overall tool life.One of the most noteworthy features of the indexable end mill is its ability to reduce machining time significantly. Equipped with multiple cutting edges on each insert, it can accomplish multiple cutting operations in a single pass. This drastically reduces the number of machining cycles required, resulting in faster production times and increased productivity. Industries that rely heavily on metal machining, such as automotive, aerospace, and mold-making, can benefit immensely from this time-saving capability.Precision is paramount in metal machining, and the indexable end mill excels in this aspect as well. With its superior inserts, specially designed and manufactured with high-quality materials, the tool ensures exceptional accuracy and surface finish. The inserts' unique geometries and coatings allow for smooth chip evacuation, preventing chip build-up and enhancing the overall cutting performance. This results in precise cuts, reduced rework, and improved overall product quality.In addition to its efficiency and precision, the indexable end mill also prioritizes ease of use and versatility. The inserts can be easily indexed to access a fresh cutting edge, eliminating the need for complicated manual regrinding. Moreover, the tool's design allows for optimal chip flow and evacuation, reducing heat buildup and ensuring smooth operation. This versatility enables the use of the indexable end mill across various materials, from aluminum and stainless steel to hardened alloys, providing a comprehensive solution for a wide range of metalworking applications.Recognizing the importance of sustainability, [Company Name] has taken environmental considerations into account during the development of the indexable end mill. By reducing material waste through the use of replaceable inserts, the tool contributes to a more sustainable machining process. This not only saves costs but also reduces the carbon footprint associated with traditional end mills.[Company Name] has a long-standing reputation for delivering cutting-edge solutions in the metalworking industry. With the introduction of the indexable end mill, the company has once again proven its commitment to innovation and customer satisfaction. Featuring state-of-the-art technology, exceptional performance, and a focus on sustainability, this tool has garnered widespread acclaim in various sectors.Numerous companies have already adopted the indexable end mill and experienced significant improvements in their metal machining operations. The tool's efficiency and precision have led to reduced production times, enhanced product quality, and increased overall profitability. Manufacturers can now confidently rely on this advanced solution to meet the ever-growing demands of their respective industries.In conclusion, the indexable end mill has established itself as a pioneering tool in the metalworking sector. Its ability to enhance efficiency, precision, and sustainability has transformed metal machining processes. [Company Name]'s commitment to innovation and customer satisfaction shines through with this remarkable solution, further solidifying its position as a leading provider in the industry. As more companies embrace this cutting-edge technology, the future of metal machining looks promising, with increased productivity, reduced costs, and improved environmental impact.
Discover the Key Benefits of Carbide End Mill Cutters for Enhanced Precision and Efficiency
Title: Achieving Unmatched Precision: A Breakthrough in Carbide End Mill CuttersIntroduction:In the ever-evolving realm of manufacturing and engineering, one tool has consistently stood out as a fundamental component for achieving precision: the carbide end mill cutter. Renowned for its exceptional durability and cutting performance, this tool has been a staple in various industries, ranging from aerospace and automotive to general machining and fabrication. In a groundbreaking development, a leading manufacturer in the field has unveiled a new generation of carbide end mill cutters that promise to revolutionize the industry with unmatched performance and precision.Company Background:With an illustrious history spanning decades, the company has been at the forefront of manufacturing high-quality cutting tools. Drawing on extensive research and development, their team of engineers and experts have consistently pushed the boundaries of what is possible in the field of precision machining. This commitment to innovation has earned them a reputation as a trusted provider of cutting-edge solutions that meet the evolving needs of their clients.Product Overview:The latest offering from the company is a refined iteration of the carbide end mill cutter, designed using state-of-the-art technology and cutting-edge materials. This new generation of cutters exhibits enhanced performance characteristics, making them ideal for a wide range of applications and industries.Cutting-edge Design:The team behind this revolutionary tool implemented a series of design improvements to elevate performance to unprecedented levels. To optimize cutting efficiency and precision, advanced computer simulations were employed to perfect the design of the flute geometry. The result is a more efficient chip removal process, significantly reducing heat generation and potential tool wear.Furthermore, the cutter's cutting edge has undergone optimization, enabling it to deliver precise cuts for a longer period, reducing the need for frequent tool changes and contributing to seamless production processes. This innovative design has also improved the stability and rigidity of the tool, allowing for higher machining speeds without compromising precision.Enhanced Material Composition:A key factor contributing to the exceptional performance of this carbide end mill cutter lies in the advanced material composition. The manufacturer utilizes premium carbide materials that have been meticulously engineered to provide increased hardness, toughness, and wear resistance. This ensures a cutter that can withstand the demanding conditions of high-speed machining while maintaining its cutting edge for prolonged periods, ultimately reducing downtime and increasing productivity.Versatility for Diverse Applications:Recognizing the diverse requirements of modern industries, the newly launched carbide end mill cutter is available in a range of variations, including different flute designs, coatings, and cutting edge configurations. This versatility allows manufacturers to tailor the tool to their specific needs, delivering optimal results across a variety of applications such as roughing, finishing, contouring, and profiling. From soft materials like plastics and aluminum to the toughest alloys and hardened steels, this tool is designed to excel in any machining environment.Commitment to Quality and Customer Satisfaction:The company's commitment to providing the highest quality tools is exemplified not only in its advanced manufacturing processes but also in its rigorous quality control measures. Each carbide end mill cutter undergoes stringent testing, ensuring it meets the highest industry standards and consistently delivers exceptional performance.Conclusion:With the unveiling of their latest generation carbide end mill cutter, this leading manufacturer is set to redefine precision machining. Through an innovative design and advanced material composition, the tool offers unparalleled cutting performance, extended tool life, and versatile application possibilities. As the manufacturing industry continues to evolve and demand even higher levels of precision, this revolutionary cutter sets the benchmark for excellence, setting the stage for a new era of precision machining.
Quality End Mills for Efficient Milling Process
Milling Cutter End Mill Empowers Metalworking Industry with Efficiency and PrecisionGlobal industrial manufacturing is constantly evolving, seeking ways to optimize production processes and meet the increasing demands for efficiency and precision. Consequently, the milling cutter end mill has emerged as a game-changer in the metalworking industry, revolutionizing machining operations across various sectors. With its advanced engineering and cutting-edge technology, this innovative tool has proven indispensable for companies striving to stay ahead in the highly competitive market.Milling cutter end mill, developed by leading industry experts, represents a paradigm shift in metal cutting technology. Its outstanding design and impeccable performance have made it a go-to tool for a wide range of manufacturing applications. From aerospace to automotive, from medical to energy, this technological breakthrough has become an essential component of modern machining operations.One of the key features that sets the milling cutter end mill apart is its exceptional cutting capabilities. Equipped with specialized cutting teeth, it enables precise removal of material from a workpiece, resulting in highly accurate and intricate machined parts. The tool’s design allows for maximum cutter engagement, delivering enhanced material removal rates while minimizing vibration and chatter, ensuring optimal surface finish and dimensional accuracy.Furthermore, the milling cutter end mill boasts exceptional durability and longevity. Made from high-quality materials, such as solid carbide or high-speed steel, it offers extended tool life and enhanced reliability. This durability not only helps reduce downtime and maintenance costs but also ensures consistent performance even under high-stress conditions. Manufacturers can rely on this tool to deliver consistent results, day in and day out, enhancing overall productivity.The versatility of the milling cutter end mill is another aspect that makes it a highly sought-after tool. It comes in various shapes, sizes, and geometries, catering to the unique machining requirements of different industries. Whether it’s for roughing, finishing, or specialized operations, there is a milling cutter end mill suitable for every application. Manufacturers can choose from a wide array of options, including ball nose, corner radius, and square end mills, among others, to achieve the desired results.Moreover, the milling cutter end mill is complemented by advanced coatings and surface treatments, further amplifying its performance capabilities. These coatings, such as TiAlN, TiCN, and TiN, enhance tool life, reduce friction, and facilitate efficient chip evacuation. Such improvements help minimize heat generation, extend tool longevity, and increase cutting speeds, enabling manufacturers to achieve higher throughput and productivity levels.The introduction of the milling cutter end mill has transformed the metalworking industry, empowering manufacturers with the ability to meet the growing demands of efficiency, precision, and quality. By leveraging this technological marvel, companies can gain a competitive edge, produce complex components with ease, and maintain high standards of productivity. With its robust design, versatility, and exceptional performance, the milling cutter end mill has become an indispensable tool for industries worldwide.One company at the forefront of this technological advancement is {}. With a rich history in precision engineering and a commitment to innovation, they have spearheaded the development of state-of-the-art milling cutter end mills. Through tireless research, cutting-edge manufacturing techniques, and collaboration with industry experts, they have successfully created a range of highly efficient and reliable tools that have transformed metal cutting operations.The company prides itself on adhering to the strictest quality standards, ensuring that each milling cutter end mill delivers exceptional performance and reliability. They prioritize customer satisfaction, offering tailored solutions to meet specific machining requirements and providing ongoing support to maximize tool longevity and performance.Through partnerships with leading manufacturers and distributors worldwide, {} has made its milling cutter end mills accessible to a wide customer base, enabling companies across the globe to benefit from this groundbreaking tool. Their commitment to continuous improvement and development guarantees that they remain at the forefront of manufacturing technology, consistently delivering solutions that enable businesses to excel in their respective industries.In conclusion, the milling cutter end mill has emerged as a vital tool in the metalworking industry, driving efficiency, precision, and productivity to new heights. With its cutting-edge design, durability, versatility, and performance-enhancing coatings, it has revolutionized machining operations across various sectors. Companies like {} have played a significant role in bringing this innovative tool to the market, empowering manufacturers to meet the evolving demands of the modern industrial landscape. As the metalworking industry continues to evolve, the milling cutter end mill remains a cornerstone of progress, helping businesses thrive in an increasingly competitive global market.
What is a Reamer Tool and How is it Used in Metalworking?
Reamer: The Rotary Cutting Tool for Accurate Hole EnlargementWhen it comes to precision drilling, there's no substitute for the humble reamer. This specialized rotary cutting tool is designed to enlarge and finish holes with accuracy and finesse, making it an essential component in several industries, from automotive and aerospace to medical and construction.A reamer works by spinning around its axis and removing thin layers of material from the walls of a previously drilled, bored, or cored hole. Its shape can be cylindrical or conical, depending on the desired hole dimensions and tolerances. However, unlike a drill bit or a boring tool, a reamer cannot initiate a hole by itself. It requires a pre-existing one as a starting point.The secret of a reamer's precision lies in its flutes or grooves. These longitudinal channels cut into the reamer's surface help guide the tool through the hole and remove the chips or shavings that result from the cutting action. Typically, reamers have eight flutes, though other numbers are possible, depending on the size, shape, and material of the hole.In addition to the flutes, reamers can have other features that enhance their cutting performance and durability. For example, they may have a coating or treatment that reduces friction or wear, or a chamfer or counterbore that eases the entry and exit of the tool. Moreover, reamers can be made from various materials, such as high-speed steel, carbide, or diamond, depending on the specific application and budget.Despite their apparent simplicity, reamers require skilled operators and proper maintenance to ensure optimal results. A reamer that is not centered, aligned, or lubricated correctly can produce out-of-round, tapered, or rough holes, which can compromise the functionality and safety of the final product. Therefore, it's vital to follow the manufacturer's recommendations and guidelines when selecting, using, and caring for reamers.One of the leading reamer manufacturers in the world is (removed for confidentiality), a company that has been delivering innovative cutting tools and solutions for over 100 years. Founded in (removed for confidentiality), (removed) has evolved from a small workshop to a global enterprise, serving customers in over 80 countries and employing thousands of people worldwide.(removed) produces a wide range of reamer types, such as hand reamers, machine reamers, chucking reamers, and adjustable reamers, as well as custom-made ones for specific applications. Its reamers can handle different materials, including steel, aluminum, brass, plastic, and composite, and work well in diverse environments, from high-speed machining to manual repair.What sets (removed) apart from its competitors is its commitment to innovation, quality, and customer service. Its research and development team is constantly exploring new materials, coatings, and geometries to improve the performance and versatility of its cutting tools. Moreover, (removed) has a stringent quality control system that ensures every reamer meets the highest standards of accuracy, consistency, and reliability.Furthermore, (removed) has a customer-centric approach that emphasizes communication, customization, and support. Its technical sales representatives work closely with clients to understand their specific needs and challenges and recommend the best reamer solution for their application. Additionally, (removed) offers after-sales services, such as reconditioning, resharpening, and repairing, to extend the lifespan and value of its reamers.In conclusion, reamers may seem like a simple tool, but they play a critical role in many industries that require precise hole enlargement and finishing. With the right design, material, and maintenance, reamers can deliver exceptional results and contribute to the quality, efficiency, and safety of various products and systems. (Removed) is a testament to this, as it continuously strives to innovate, excel, and delight its customers with its cutting-edge reamer solutions.
Revamp Your Workshop with High-Quality Cutting Tools: All You Need to Know About Mills
Cutting Tools Mills Revolutionizes the Industry with Innovative TechnologyIn today's competitive manufacturing landscape, innovation is key. Businesses are constantly seeking cutting-edge solutions to enhance their operations and drive efficiency. Cutting Tools Mills, a renowned player in the cutting tools industry, is making waves with its groundbreaking technology that is revolutionizing the sector. With its unwavering focus on quality and customer satisfaction, Cutting Tools Mills is leading the way in delivering cutting-edge products to meet the evolving needs of manufacturing companies worldwide.Established in 1990, Cutting Tools Mills has amassed years of industry experience and expertise. The company operates with the core philosophy of continuous improvement, always striving to push the boundaries of what is possible. This approach has led to the development of state-of-the-art tools that have set new benchmarks in performance and durability.One of the company's flagship products is its high-speed cutting tools. Leveraging advanced materials and cutting-edge manufacturing techniques, Cutting Tools Mills has successfully crafted tools that can withstand extreme conditions and deliver exceptional results. These high-speed tools are designed to operate at elevated RPMs, resulting in precise and efficient machining. Additionally, they boast enhanced wear resistance, enabling them to endure rigorous manufacturing processes without compromising on performance.The innovative technology behind Cutting Tools Mills' products extends beyond high-speed cutting tools. The company also offers a wide range of milling tools that cater to diverse machining requirements. From face milling to profile milling and everything in between, Cutting Tools Mills has developed a comprehensive suite of tools that empower manufacturers to achieve superior results. By investing heavily in research and development, the company stays ahead of industry trends and continuously introduces new and improved milling solutions.Quality is embedded in the DNA of Cutting Tools Mills. The company adheres to strict quality control processes to ensure that every product leaving its facility is of the highest standard. From raw material procurement to the final stages of production, each step is meticulously monitored to guarantee consistency and reliability. This commitment to quality has earned Cutting Tools Mills a reputation for excellence, making it the preferred choice of manufacturing companies across the globe.Furthermore, Cutting Tools Mills maintains a customer-centric approach that underpins its success. The company understands that every manufacturing process is unique, and therefore, offers tailored solutions that perfectly align with individual customer requirements. Whether it's a small-scale operation or a large-scale manufacturing facility, Cutting Tools Mills has the expertise and capabilities to provide comprehensive cutting solutions that drive productivity and efficiency.To solidify its position as a thought leader in the industry, Cutting Tools Mills actively engages in knowledge sharing initiatives. The company regularly conducts seminars and workshops to educate manufacturers on best practices and the latest advancements in cutting tools technology. By fostering an environment of collaboration and learning, Cutting Tools Mills not only supports its customers but also contributes to the overall growth of the industry.Looking ahead, Cutting Tools Mills is committed to pushing the boundaries of innovation and continuing its legacy of delivering premium cutting solutions. The company envisions a future where manufacturing processes are efficient, reliable, and sustainable. By investing in cutting-edge technology and nurturing a culture of excellence, Cutting Tools Mills is poised to spearhead the next wave of advancements in the cutting tools industry.In conclusion, Cutting Tools Mills has firmly established itself as a global leader in the cutting tools industry. Through its unwavering commitment to innovation, quality, and customer satisfaction, the company has revolutionized the sector with its groundbreaking technology. As the manufacturing landscape continues to evolve, Cutting Tools Mills remains at the forefront, empowering businesses with cutting-edge solutions that maximize efficiency and productivity.
Top-Quality Two-Flute Upcut CNC Bits for Excellent Routing Results
Two Flute Upcut CNC Router Bits: The Perfect Solution for Smooth and Accurate RoutingThe world of CNC routing is an exciting one, with computer-controlled machines helping businesses and individuals create intricate designs with the utmost precision. However, to achieve the desired results, one crucial component that requires close attention is the router bit. Your choice of router bit can make or break the quality of your finished product. This is where two flute upcut CNC router bits come into play.What Are Two Flute Upcut CNC Router Bits?Two flute upcut CNC router bits are a specific type of cutting tool designed for use in CNC machines. They feature two spiral upcut flutes, which means that as the bit rotates, it pulls chips up and away from the workpiece. The upcut design helps to maintain a smooth and clean edge on the material, reducing fraying and leaving a polished finish.Benefits of Two Flute Upcut CNC Router BitsThere are several benefits to using two flute upcut CNC router bits, some of which include:1. Clean and Smooth FinishUpcut bits tend to offer a cleaner cut than their downcut counterparts. The upcut design pulls chips up and out of the way, reducing the chance of chip buildup. This results in less fraying, a smoother finish, and less clean-up work required after routing.2. Reduced Heat BuildupAnother advantage of two flute upcut CNC router bits is that they have an optimized geometry that helps reduce the amount of heat generated during cutting. This is important as excessive heat can lead to premature wear and tear on the bit, as well as cause cracking and warping of the material being routed.3. VersatilityTwo flute upcut CNC router bits are suitable for most routing applications, meaning that they can be used on a wide range of materials. These include wood, plastic, and some soft metals.Things to Consider When Choosing Two Flute Upcut CNC Router BitsWhen it comes to selecting the right two flute upcut CNC router bit for your project, there are several factors to keep in mind. These include:1. Bit SizeThe size of the bit you choose will depend on the scale of your project and the material you're using. Smaller bits are suitable for intricate work with fine details, while larger bits are ideal for roughing out and removing larger amounts of material quickly.2. Bit MaterialThe material your bit is made from will impact its durability and cutting performance. Common materials used to make router bits include carbide, high-speed steel (HSS), and cobalt.3. Flute LengthThe flute length of the bit refers to the length of the cutting portion. Longer flute lengths are better for deeper cuts, while shorter flute lengths work well for shallower cuts.Tips for Using Two Flute Upcut CNC Router BitsHere are some tips to help you get the most out of your two flute upcut CNC router bit:1. Choose the Right Speed and Feed RateThe speed and feed rate at which you run your CNC machine can have a significant impact on the performance of your bit. Be sure to follow the manufacturer's recommended speed and feed rate for your specific bit.2. Keep Your Bit SharpDull bits can cause excessive heat buildup and lead to a rough finish. Be sure to sharpen your bit regularly to maintain optimal performance.3. Clean Your Bit After UseAfter routing, be sure to clean your bit thoroughly. This will help to prevent buildup of debris and extend the life of your bit.ConclusionTwo flute upcut CNC router bits are an excellent choice for those seeking smooth and accurate routing results. Their upcut design and optimized geometry provide clean cuts and reduced heat buildup, resulting in a polished finish. When choosing a bit, be sure to consider factors such as size, material, and flute length. By following these tips, you can maximize the life and performance of your two flute upcut CNC router bit.